4 min read
How Communication Affects Supply Chains and How To Improve It
Katie Dalrymple
:
May 22, 2024
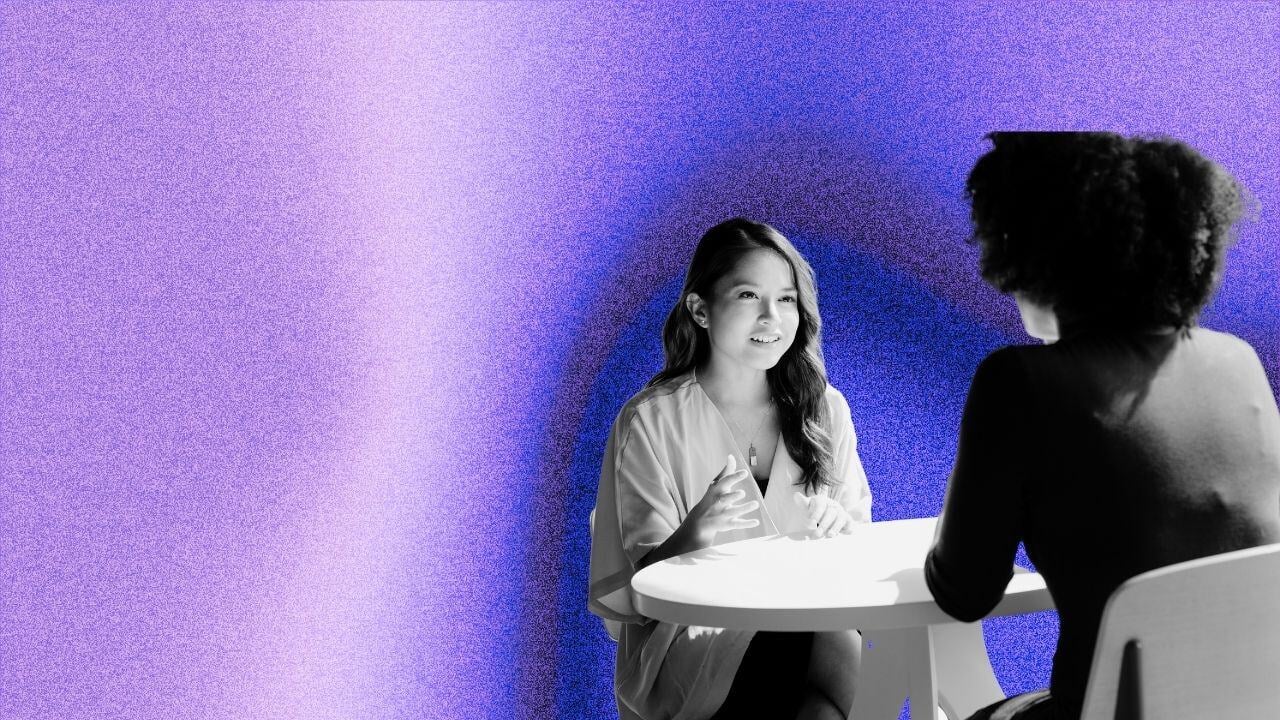
Creating a clear line of communication throughout your supply chain operations will positively impact your supply chain outcomes.
It can be complicated to make sure the entire process from procurement to last-mile delivery is seamless. Ensuring that all inventory goes to the right place at the right time can also be rather fickle. That’s why you need end-to-end communication throughout your logistics operations to connect the dots of your entire supply chain.
Creating an effective inventory process with thorough visibility and communication requires buy-in from a variety of stakeholders. Using technology to manage workflows and operations will ensure inventory doesn’t fall through the cracks. Without inventory management, your business can miss out on many revenue opportunities. In fact, about 43% of small businesses are still using old-fashioned inventory tracking methods or don’t track inventory at all, leading to a gap in their operational communications.
When it comes to revenue and industrial growth it all circles back to having proper logistical communication.
What Happens When Your Supply Chain Lacks Communication?
It’s essential to keep up with the future of the industry, especially with the increasing competition and consumer demands of today. The numerous people and businesses it takes to run a supply chain leaves room for huge amounts of miscommunication or missing data.
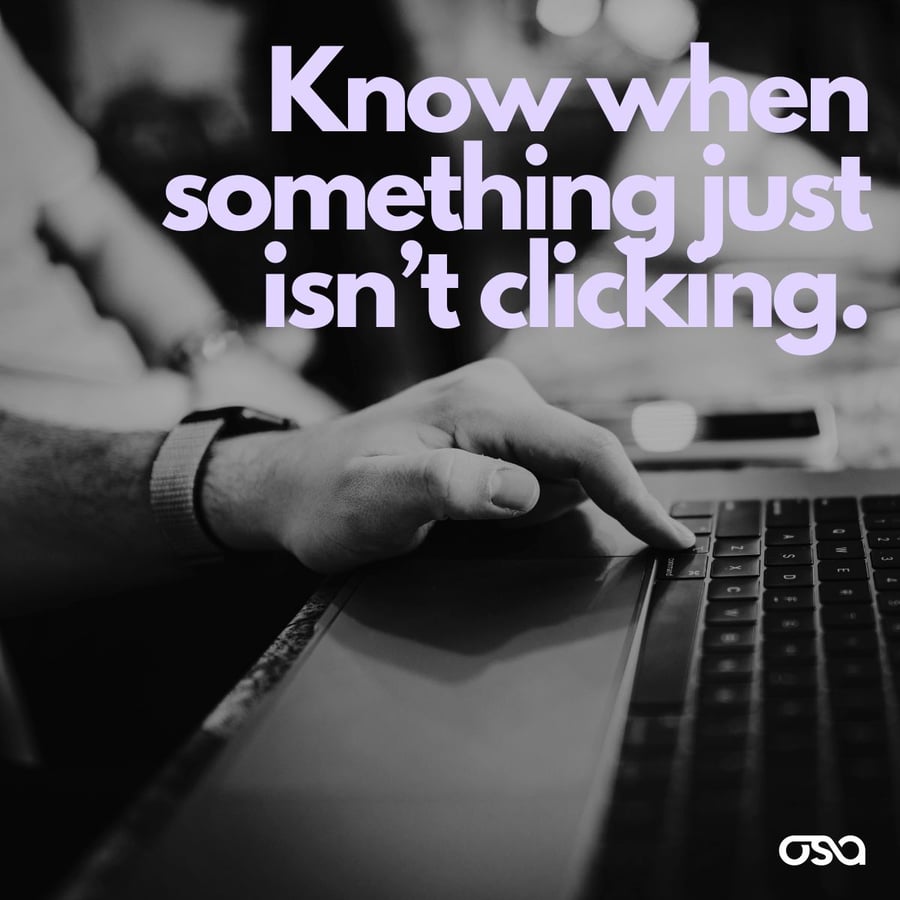
The first step to avoiding mishaps is understanding who all the parties involved are. Here are some most common supply chain team members:
- Internal Operations Team: Manages and optimizes the production and delivery processes within a company to ensure efficiency and effectiveness.
- Internal Accounting Team: Handles financial records, budgeting, and financial reporting within the organization.
- Internal Finance Team: Oversees the company's financial planning, analysis, and investment strategies.
- Internal Shipping Team: Coordinates the transportation of goods from the company to customers or other destinations.
- Internal Logistics Team: Manages the flow of goods, information, and resources within the company to ensure timely delivery and inventory control.
- Retail Employees: Work in retail stores to assist customers, manage inventory, and ensure smooth sales operations.
- Warehouse Location Employees: Handle the storage, management, and movement of goods within a warehouse facility.
- Consignees: Individuals or entities that receive goods shipped to them.
- Consignors: Individuals or entities that send goods to a consignee.
- Agents at Both Origin and Destination: Representatives who manage and facilitate the shipping process at both the starting and ending points of a shipment.
- Customs Agents: Government officials responsible for regulating and inspecting goods entering or leaving a country to ensure compliance with laws and regulations.
- Freight Forwarders: Companies or individuals that arrange and coordinate the transportation of goods on behalf of shippers, including handling documentation and logistics.
- Shipping Carrier: Companies that physically transport goods from one location to another via various modes of transport such as sea, air, or land.
Additionally, knowing where the most common miscommunications happen will help address immediate concerns. Here are some of the top issues:
- Lost Inventory: Goods that are missing or unaccounted for within the supply chain, leading to discrepancies in stock levels.
- Late Deliveries: Shipments that do not arrive at their destination within the expected or agreed-upon timeframe.
- Storage Fees: Charges incurred for keeping goods in a storage facility, such as a warehouse, for a certain period.
- Not Able to Plan Inventory Turnover: Difficulty in accurately predicting the rate at which inventory is sold and replaced, leading to inefficiencies in stock management.
- Not Able to Properly Predict All Logistics Costs: Inability to accurately forecast the expenses associated with the movement and storage of goods throughout the supply chain.
- Bad Public Reviews: Negative feedback from customers can harm the company's reputation and deter potential buyers.
- Unsatisfied Customers: Customers who are unhappy with the products or services received, often due to issues such as poor quality, delays, or inadequate support.
- Tension Within the Supply Chain Relationships: Strained interactions and conflicts between different parties involved in the supply chain, such as suppliers, manufacturers, and retailers.
- No Traceability: Lack of ability to track the origin, movement, and history of products throughout the supply chain, leading to challenges in quality control and accountability.
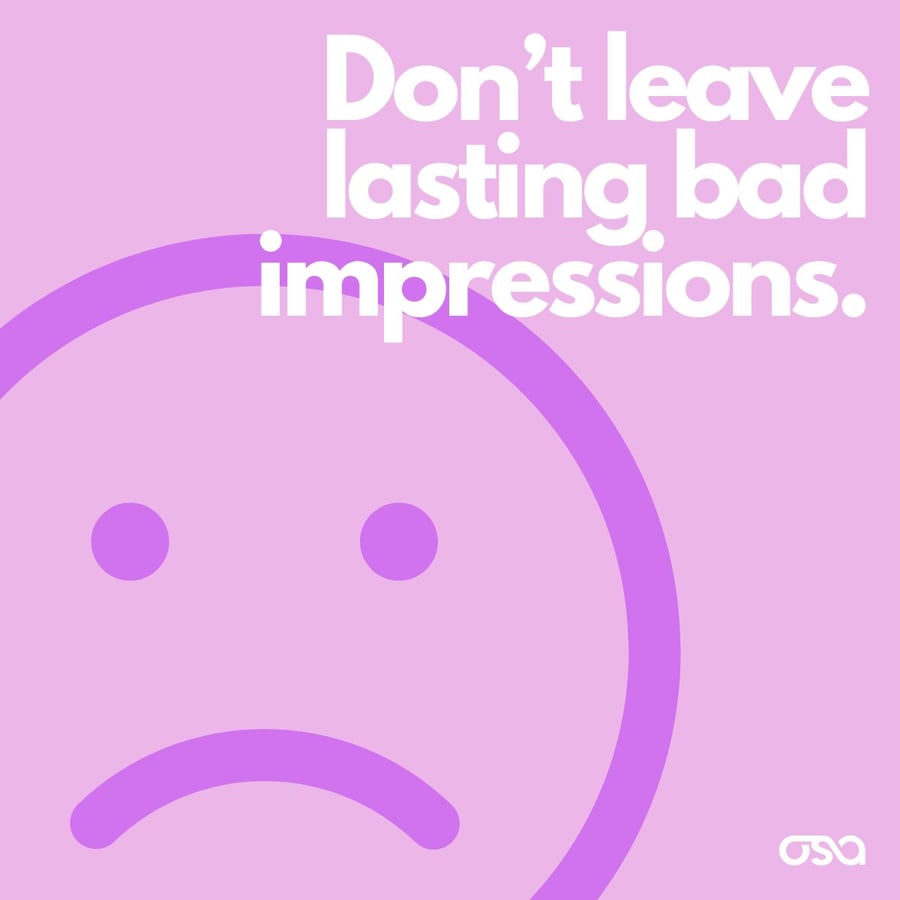
With the proper technology and infrastructure, communication issues can quickly be sorted out so your supply chain is ready to run smoother than ever.
How Good Communication Can Help Your Supply Chain
The infrastructure of the shipping and delivery industry is still adjusting to the requirements and the sheer scale of the modern day. Today, most businesses can’t simply settle with the fact that they won’t be able to satisfy all customers or complete all deliveries. To help alleviate these issues has led more brands and retailers to outsource their services to third-party logistics (3PL) businesses and other logistic services companies.
Utilizing tools and resources to help with the positive direction in communications, businesses can expect not only to see deliveries stop falling through the cracks but also a multitude of other improvements:
- Productivity increases due to connected employees, real-time visibility, and a better understanding of the system.
- Workplace culture improves, people want to know what’s going on!
- Positive relations with external companies, partners, and vendors can lead to decreased lead times and increased revenue.
- Improved profits and bottom lines, when your supply chain is operating smoothly everything improves!
- Increased customer satisfaction
How To Implement Communication Into Your Supply Chain With Collaborative Visibility
So, how do brands and retailers take the first step to improving communication across their supply chain with their 3PL partners?
One of the first pieces of advice we give is to gain access to real-time data. This data can be gathered from existing supply chain systems you have in place. Once you have a complete list, consider integrating these via API integrations to Collaborative Visibility Technology. Once implemented into your existing process, you will have a one-stop-shop for all things supply chain related.
The Osa Collaborative Visibility Platform uses AI-powered unified commerce technology to transform supply chain operations by providing an all-in-one platform for enhanced visibility and collaboration. This innovation allows businesses to streamline processes, reduce costs, and boost customer satisfaction.
A completely connected supply chain will offer brands and retailers the opportunity to create a unified product journey and fill in the missing communication gaps for their customers.
Let’s talk to learn how you can utilize Collaborative Visibility to create across-the-board communication in your supply chain.