9 min read
Warehouse Management Principles for Mastering Warehouse Operations
Osa Commerce
:
May 20, 2024

In the realm of logistics and supply chain management, the efficiency of warehouse operations stands as a cornerstone for success. Effective warehouse management principles not only streamline processes but also contribute significantly to cost reduction, customer satisfaction, and overall business growth. In this comprehensive guide, we delve into the fundamental principles that govern warehouse management, shedding light on best practices, innovative approaches, and the importance of leveraging technology for optimal results for third-party logistics warehouses (3PLs) and their brand and retailer customers.
Table of Contents
Control and Manage Material Movement and Storage
Streamline Transaction Processes Effectively
Integrate Warehouse Management with Order Processing
Achieve Maximum Transparency with Warehouse Innovations
Guarantee Warehouse Data Security
Employ Trained and Professional Warehouse Personnel
Conduct Regular Warehouse Equipment Quality Checks
Explore the Benefits of a Good Warehouse Layout Design
Control and Manage Material Movement and Storage
At the core of warehouse management lies the ability to control the movement and storage of goods with precision. This involves strategic organization of inventory within the warehouse to facilitate easy access, efficient picking, optimized packing, and timely replenishment. This includes implementing efficient processes for receiving, storing, and retrieving materials, as well as ensuring proper inventory management.
Utilizing technology including a robust inventory management system, employing barcode technology, and adopting lean principles are instrumental in achieving this objective. By maintaining accurate inventory records and implementing systematic storage strategies such as ABC analysis or zone picking, organizations can minimize stockouts, reduce carrying costs, and enhance operational efficiency.
Technology platforms should accurately track the quantity and location of materials, enabling warehouse staff to quickly locate and retrieve items as needed. Additionally, it should provide real-time visibility into inventory levels, allowing for better planning and decision-making.
Effective warehouse management involves implementing proper material handling techniques. This includes using appropriate equipment and tools to safely and efficiently move materials within the warehouse. By ensuring that materials are handled properly, warehouses can minimize the risk of damage or loss, resulting in cost savings and improved customer satisfaction.
Controlling the movement and storage of materials is a basic principle of warehouse management. By implementing efficient processes, utilizing inventory management systems, and practicing proper material handling techniques, warehouses can optimize their operations and achieve greater success.
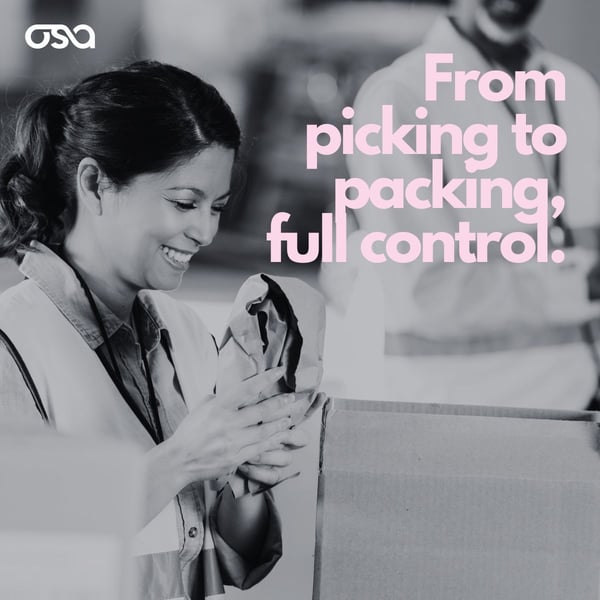
Quickly Process Sales Orders
The ability to process sales orders with speed and accuracy is paramount. Efficient order fulfillment not only satisfies customer demands promptly but also enhances brand reputation and fosters repeat business. Leveraging advanced warehouse management systems (WMS) equipped with order processing functionalities can automate and streamline order fulfillment processes, from order capture to shipment. By optimizing order picking routes, minimizing order processing times, and integrating with transportation management systems (TMS), organizations can expedite order fulfillment while minimizing errors and reducing operational costs.
To process sales orders speedily, warehouses should implement streamlined order fulfillment processes. This includes having well-defined workflows for order processing, from receiving the order to picking, packing, and shipping the items. By eliminating bottlenecks and unnecessary steps in the process, warehouses can reduce order processing time and improve efficiency.
Additionally, leveraging technology can significantly speed up the order processing process. Warehouse management systems and automation tools can automate manual tasks, such as order entry and inventory updates, reducing the time required to process each order. This not only speeds up the overall process but also reduces the risk of errors and improves order accuracy.
Processing sales orders speedily is essential for effective warehouse management. By implementing streamlined processes and leveraging technology, warehouses can improve order processing time, enhance customer satisfaction, and drive business growth.
Maintain Optimum Stock Levels
Maintaining optimum stock levels is essential for balancing inventory costs with customer service levels. Striking the right balance ensures that warehouses have sufficient inventory to meet customer demand without excess stock tying up valuable capital. Employing demand forecasting techniques, safety stock calculations, and replenishment strategies such as just-in-time (JIT) inventory management can help organizations optimize stock levels effectively. Additionally, real-time visibility into inventory levels through WMS dashboards enables proactive decision-making, facilitating timely replenishment and preventing stockouts or overstock situations.
To keep optimum stock levels, warehouses should have a clear understanding of demand patterns and inventory turnover rates. By analyzing historical sales data and market trends, warehouses can forecast future demand and adjust their stock levels accordingly. This prevents stockouts and overstock situations, both of which can have negative impacts on customer satisfaction and warehouse profitability.
Implementing inventory management as a part of a collaborative visibility platform can greatly facilitate the function of keeping optimum stock levels. These systems can provide real-time visibility into inventory levels, allowing warehouses to monitor stock levels and make informed replenishment decisions. They can also generate automated reorder alerts when stock levels fall below a certain threshold, ensuring timely replenishment.
3PL warehouses must keep optimum stock levels as a critical function of warehouse management. By accurately forecasting demand, implementing inventory management systems, and monitoring stock levels, warehouses can optimize their inventory levels and improve operational efficiency for their customers and consumers.
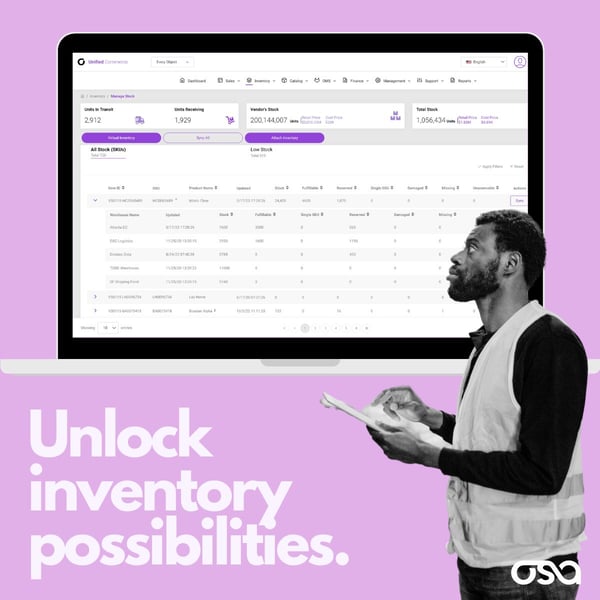
Streamline Transaction Processes Effectively
Efficient processing of associated transactions is essential as it ensures accurate and timely recording of all warehouse activities.
As you know, warehouses handle various transactions such as receiving, picking, packing, and shipping. Efficiently managing these transactions is paramount to overall warehouse productivity. Utilizing barcode scanning, RFID technology, and mobile devices can streamline transactional processes, reduce manual errors, and improve real-time visibility into inventory movements.
Associated transactions refer to various activities that occur within the warehouse, such as receiving goods, transferring inventory, and conducting inventory counts. These transactions need to be processed efficiently to maintain accurate records and enable proper inventory management.
To process associated transactions efficiently, warehouses should implement standardized procedures and best practice workflows. This includes clearly defining the steps involved in each transaction and providing training to warehouse staff on how to execute these transactions accurately and efficiently.
Additionally, leveraging the best warehouse management systems can greatly improve the efficiency of processing associated transactions. Warehouse management systems can automate transaction recording, eliminating the need for manual data entry and reducing the risk of errors. They can also provide real-time visibility into transaction status, allowing warehouse managers to monitor and track the progress of each transaction.
Processing associated transactions efficiently is a key principle of warehouse management. By implementing standardized procedures, providing training to staff, and leveraging technology, warehouses can ensure accurate and timely recording of all warehouse activities.
Integrate Warehouse Management with Order Processing
Seamless integration between warehouse management and sales order processing is essential for optimizing inventory allocation, order fulfillment, and customer satisfaction. By synchronizing data and processes between WMS and order management systems (OMS), organizations can ensure real-time visibility into inventory availability, order status, and shipping information. This integration facilitates dynamic order promising, allowing businesses to commit accurate delivery dates and allocate inventory efficiently based on customer demand, inventory levels, and shipping constraints.
Linking warehouse management to sales order processing is essential for efficient and seamless operations—especially for warehouses offering e-commerce or omnichannel fulfillment. By integrating these two functions, warehouses can improve order fulfillment processes, enhance inventory accuracy, and optimize resource allocation.
One way to maximize transparency between warehouse management to order processing is by implementing a centralized system that connects the two functions. This platform should enable real-time data sharing between sales and warehouse teams, ensuring that inventory information is always up to date and accurate. It should also facilitate seamless order processing, from order entry to fulfillment, by automating data transfer and reducing manual tasks.
Linking warehouse management to sales order processing also allows for better resource planning and allocation. By having visibility into sales forecasts and order volumes, warehouses can adjust their staffing levels and inventory levels accordingly. This improves operational efficiency and reduces the risk of stockouts or overstock situations.
Complete transparency between warehouse management and order processing is a crucial principle for effective warehouse operations. By integrating these functions and implementing a centralized system, warehouses can streamline processes, improve inventory accuracy, and optimize resource allocation.
Achieve Maximum Transparency with Warehouse Innovations
Embracing warehouse innovations such as internet of things (IoT) sensors, predictive analytics, artificial intelligence (AI), and machine learning algorithms enhances transparency and visibility across warehouse operations. By leveraging IoT-enabled devices to monitor inventory levels, equipment performance, and environmental conditions in real-time, organizations can proactively identify issues, optimize resource utilization, and improve decision-making. Additionally, predictive analytics capabilities enable organizations to forecast demand, anticipate maintenance needs, and optimize warehouse layouts for maximum efficiency.
By leveraging innovative technologies and practices, warehouses can improve operational visibility, enhance efficiency, and reduce errors. One way to ensure transparency is by implementing a collaborative visibility platform that houses WMS, OMS, integrations and more to provide real-time visibility into warehouse operations. These platforms can easily track inventory levels, monitor order statuses, and generate reports on key performance indicators (KPIs). They enable warehouse managers to make informed decisions and take proactive measures to optimize operations.
Additionally, innovative technologies such as barcode scanning, RFID tagging, and automation can greatly enhance transparency in the warehouse. These technologies enable accurate and efficient tracking of inventory, reduce manual errors, and improve overall operational efficiency.
Ensuring the highest level of transparency through warehouse innovations is a critical principle of effective warehouse management. By implementing collaborative solutions such as WMS, leveraging innovative technologies, and fostering a culture of transparency, warehouses can improve operational visibility, enhance efficiency, and drive business growth.
Guarantee Warehouse Data Security
With the increasing digitization of warehouse operations, safeguarding warehouse data against cyber threats and unauthorized access is paramount. Implementing technology that offers robust cybersecurity measures, including firewalls, encryption protocols, and access controls, helps mitigate the risk of data breaches and ensure the confidentiality, integrity, and availability of critical warehouse information. Regular security audits, employee training programs, and adherence to industry best practices further bolster data safety and protect against evolving cyber threats.
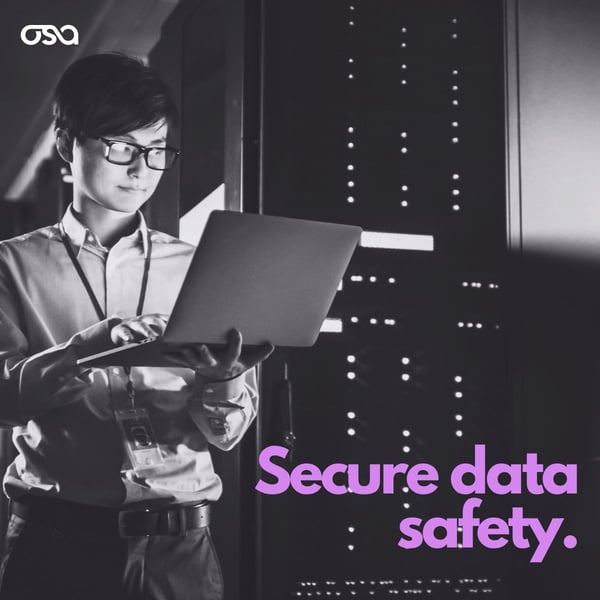
Warehouse data includes sensitive information such as customer orders, inventory records, and financial data. Protecting this data from unauthorized access, loss, or corruption is essential for maintaining operational efficiency and customer trust. Working with supply chain technology partners that utilize robust data security measures. Warehouses may also need to use secure networks, implement firewalls and intrusion prevention systems, and use technology that offers continuous enhancements to address any vulnerabilities.
Additionally, warehouse personnel should receive training on data security best practices, such as creating strong passwords, recognizing phishing attempts, and following proper data handling procedures. By promoting a culture of data security awareness, warehouses can reduce the risk of data breaches and ensure the safety of sensitive information.
Warehouse data safety is an important principle of effective warehouse management. By implementing robust data security measures, establishing data backup and recovery procedures, and promoting data security awareness among staff, warehouses can protect sensitive information, maintain operational efficiency, and build trust with customers.
Employ Trained and Professional Warehouse Personnel
Investing in the training and development of warehouse personnel is essential to ensure proficiency in handling tasks and operating equipment. From inventory management and order picking to equipment operation and safety protocols, well-trained personnel contribute to higher productivity, lower error rates, and improved customer satisfaction.
Having trained and professional storage personnel is crucial for effective warehouse management. Warehouse staff play a key role in ensuring smooth operations, accurate inventory management, and efficient order fulfillment.
To have trained and professional storage personnel, warehouses should invest in proper training programs. This includes providing training on warehouse processes and procedures, material handling techniques, and safety protocols. By equipping staff with the necessary knowledge and skills, warehouses can minimize errors, reduce accidents, and improve operational efficiency.
Additionally, regularly evaluating the performance of storage personnel is essential. This allows warehouses to identify areas for improvement, provide constructive feedback, and recognize and reward high-performing employees. By nurturing a culture of continuous improvement, warehouses can ensure that their storage personnel are always striving to excel in their roles.
Trained personnel is a fundamental principle of effective warehouse management. By investing in training programs, fostering professionalism, and evaluating performance, warehouses can optimize their operations and achieve greater success.
Conduct Regular Warehouse Equipment Quality Checks
Maintaining the reliability and performance of warehouse equipment is essential for minimizing downtime, maximizing throughput, and ensuring workplace safety. Conducting regular quality checks, preventive maintenance, and equipment inspections help identify potential issues early, mitigate risks, and extend the lifespan of critical assets. Additionally, investing in state-of-the-art equipment, such as automated storage and retrieval systems (AS/RS) and robotic palletizers, enhances efficiency, accuracy, and scalability in warehouse operations.
To ensure warehouse equipment is in good working condition, warehouses should establish a regular maintenance schedule. This includes conducting routine inspections, cleaning, and lubrication of equipment, as well as addressing any issues or malfunctions promptly. By proactively maintaining equipment, warehouses can minimize downtime, reduce the risk of accidents, and extend the lifespan of their assets.
Investment in high-quality equipment from reputable manufacturers that is more durable, reliable, and efficient, can result in improved operational performance and reduced maintenance costs in the long run. In addition, providing proper training to warehouse staff on equipment operation and safety is crucial. When staff are knowledgeable and skilled in using equipment, they can operate it safely and efficiently, minimizing the risk of accidents or damage to equipment.
By establishing maintenance schedules, investing in quality equipment, and providing training to staff, warehouses can optimize their material handling processes and improve operational efficiency.
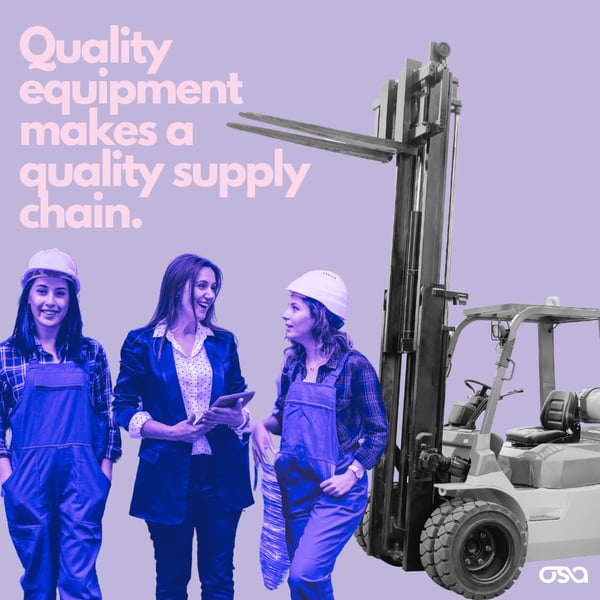
Explore the Benefits of a Good Warehouse Layout Design
A well-planned warehouse layout design is pivotal in boosting productivity, slashing travel time, and maximizing space efficiency. Through strategic placement of storage zones, aisle configurations, and workflow paths, businesses can alleviate congestion, diminish picking errors, and optimize material movement. Moreover, a thoughtfully designed warehouse layout upholds ergonomic standards, fosters safety, and ensures the effective utilization of labor and equipment resources.
Optimized Space Utilization:
A prime benefit of a well-structured warehouse layout is the efficient utilization of available space. By tactically arranging storage areas, aisles, and workstations, warehouses can make the most of their square footage, minimizing wastage. This facilitates smoother material flow, curtails unnecessary travel time, and enhances overall productivity.
Enhanced Safety:
A meticulously designed warehouse layout contributes to a safer work environment, mitigating the risk of accidents. Clear aisles, designated walkways, and appropriate signage aid in averting collisions and tripping hazards, fostering a secure workplace for warehouse personnel and reducing the likelihood of injuries.
Improved Inventory Management:
A well-organized warehouse layout promotes better inventory visibility and accuracy. Through logical inventory arrangement and the implementation of proper labeling and signage, warehouses can expedite item retrieval and reduce the time spent on order picking. This, in turn, enhances order accuracy and customer satisfaction.
Effective Workforce:
An adeptly designed warehouse layout enhances employee efficiency and safety by minimizing unnecessary movement and mitigating accident risks. By optimizing the placement of workstations, storage areas, and equipment, organizations can streamline workflows, alleviate fatigue, and bolster employee morale and satisfaction.
Material Handling Equipment:
Investing in appropriate material handling equipment—such as forklifts, pallet jacks, and conveyor systems—is indispensable for maximizing productivity and minimizing labor costs. By selecting equipment that aligns with operational needs and warehouse layout design, businesses can streamline material handling processes, enhance throughput, and mitigate the risk of injuries or accidents.
Correct Warehouse Layout:
A well-tailored warehouse layout optimizes space usage, minimizes travel distances, and augments operational efficiency. Through the segregation of storage areas based on product characteristics, demand patterns, and handling requirements, organizations can expedite picking processes, alleviate congestion, and enhance inventory visibility. Additionally, incorporating flexibility into the warehouse layout facilitates easy reconfiguration to accommodate evolving business demands and seasonal fluctuations in demand.
Conclusion
Effective warehouse management is essential for optimizing supply chain performance, enhancing customer satisfaction, and driving business success. By implementing the principles outlined in this guide, businesses can streamline warehouse operations, improve inventory accuracy, and gain a competitive edge in today's dynamic marketplace. From leveraging advanced technologies to investing in employee training and infrastructure, adopting a holistic approach to warehouse management can yield significant long-term benefits and pave the way for sustainable growth.
The basic principles of warehouse management encompass controlling material movement, processing orders efficiently, maintaining optimal stock levels, ensuring transparency through innovation, prioritizing data security, investing in trained personnel, and regularly assessing equipment quality. By adhering to these principles and leveraging technology and best practices, organizations can optimize warehouse operations, enhance customer satisfaction, and drive business success in a highly competitive marketplace.