11 min read
Mastering Order Orchestration for Efficient Supply Chain Operations
Chelsea Mori
:
June 27, 2024
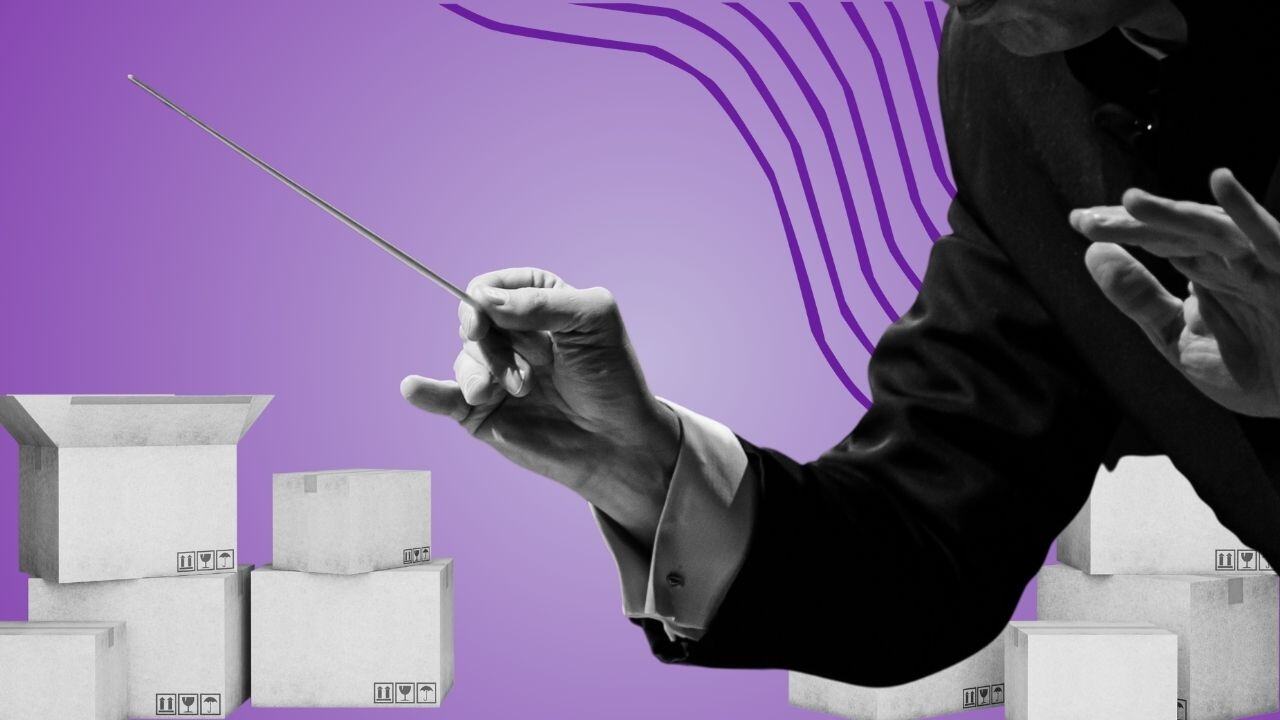
Explore the key strategies and best practices for mastering order orchestration to enhance supply chain efficiency and optimize e-commerce and omnichannel operations.
Table of Contents
What is the Difference Between Order Orchestration and Order Management?
Key Differences of Order Orchestration and Order Management
Objectives of Order Orchestration
Benefits of Order Orchestration
Common Order Orchestration Rules
Steps Involved in the Order Orchestration Process
What is Order Orchestration?
Order orchestration is an automated process that manages the entire lifecycle of an order— from its inception to fulfillment. It involves coordinating the critical activities across different supply chain systems and departments to ensure that an order is processed efficiently and accurately. This includes managing inventory, processing payments, handling shipping logistics, and ensuring customer communication.
The primary goal of order orchestration is to streamline operations, reduce errors, and enhance customer satisfaction. It enables e-commerce brands or retailers to handle multiple orders simultaneously while maintaining visibility and control over the entire process. Key components include order capture, inventory management, order processing, shipping, and delivery.
What is the Difference Between Order Orchestration and Order Management?
Order orchestration and order management are closely related concepts—particularly in e-commerce and supply chain management. Yet, they each serve distinct purposes and involve different processes.
Order management is the comprehensive process of capturing, tracking, and fulfilling customer orders. It encompasses all activities from when a customer places an order to when the product is delivered. Many supply chain businesses use Order Management System (OMS) to capture the entire lifecycle of an order
Order orchestration, on the other hand, refers to the coordination and automation of the end-to-end order fulfillment process. It involves integrating various systems and processes to collaborate a seamless execution and delivery of orders.
Key Differences of Order Orchestration and Order Management
Order orchestration systems integrate with various enterprise systems such as Enterprise Resource Planning (ERP), Customer Relationship Management (CRM), and Warehouse Management Systems (WMS). This integration ensures real-time data flow, allowing for quick decision-making and adaptability to changes in order volume or supply chain disruptions. Supply chain platforms, especially those with collaborative visibility, offer solutions that impact both order management and order orchestration.
Effective order orchestration leads to faster order fulfillment, improved accuracy, and better resource utilization. For customers, it means timely deliveries, accurate order tracking, and a smoother overall shopping experience. In an increasingly competitive and customer-centric market, order orchestration is essential for maintaining efficiency and achieving high levels of customer satisfaction.
Here are few key differences between the two:
Scope
Order management focuses on the entire order lifecycle from placement to delivery, whereas order orchestration is about the seamless integration and automation of the various steps involved in fulfilling an order.
Functionality
Order management handles the basics of order processing and fulfillment. In contrast, order orchestration aims to optimize these processes through integration, automation, and real-time visibility.
Objective
The main goal of order management is to ensure orders are processed and delivered correctly. Order orchestration seeks to enhance efficiency, reduce errors, and improve overall operational performance.
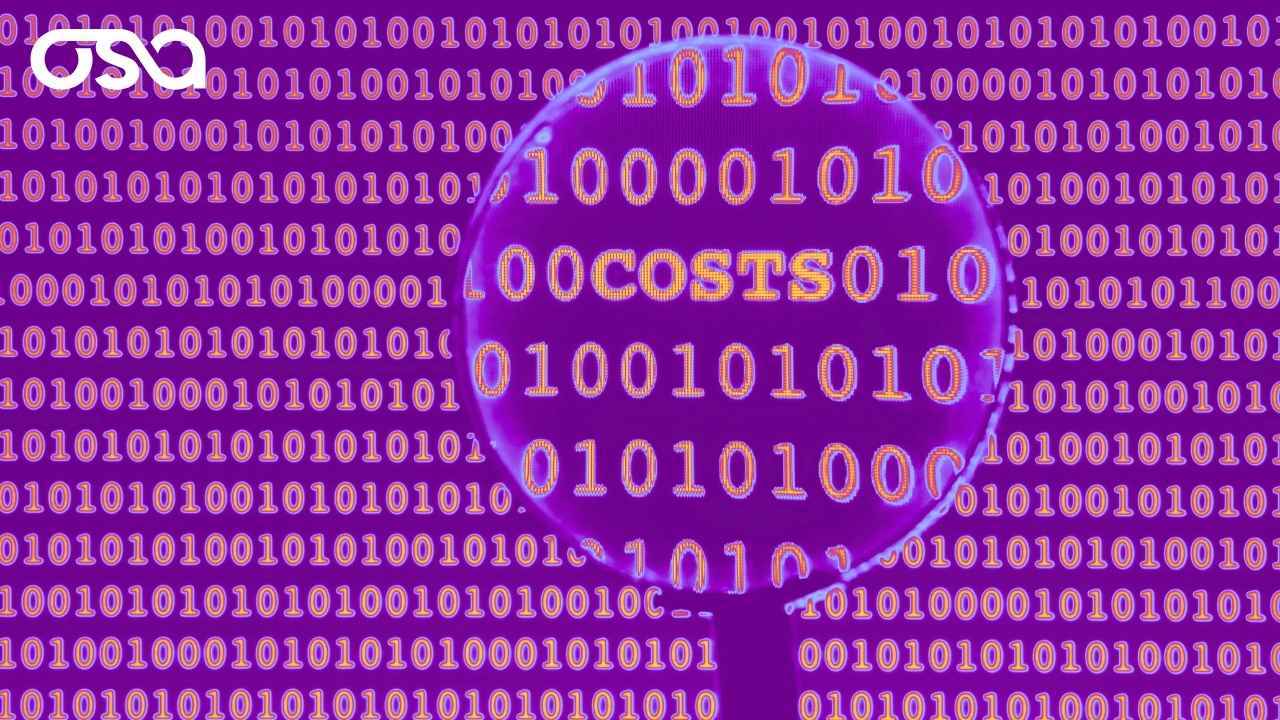
How to Reduce Logistics Costs with Supply Chain Integrations
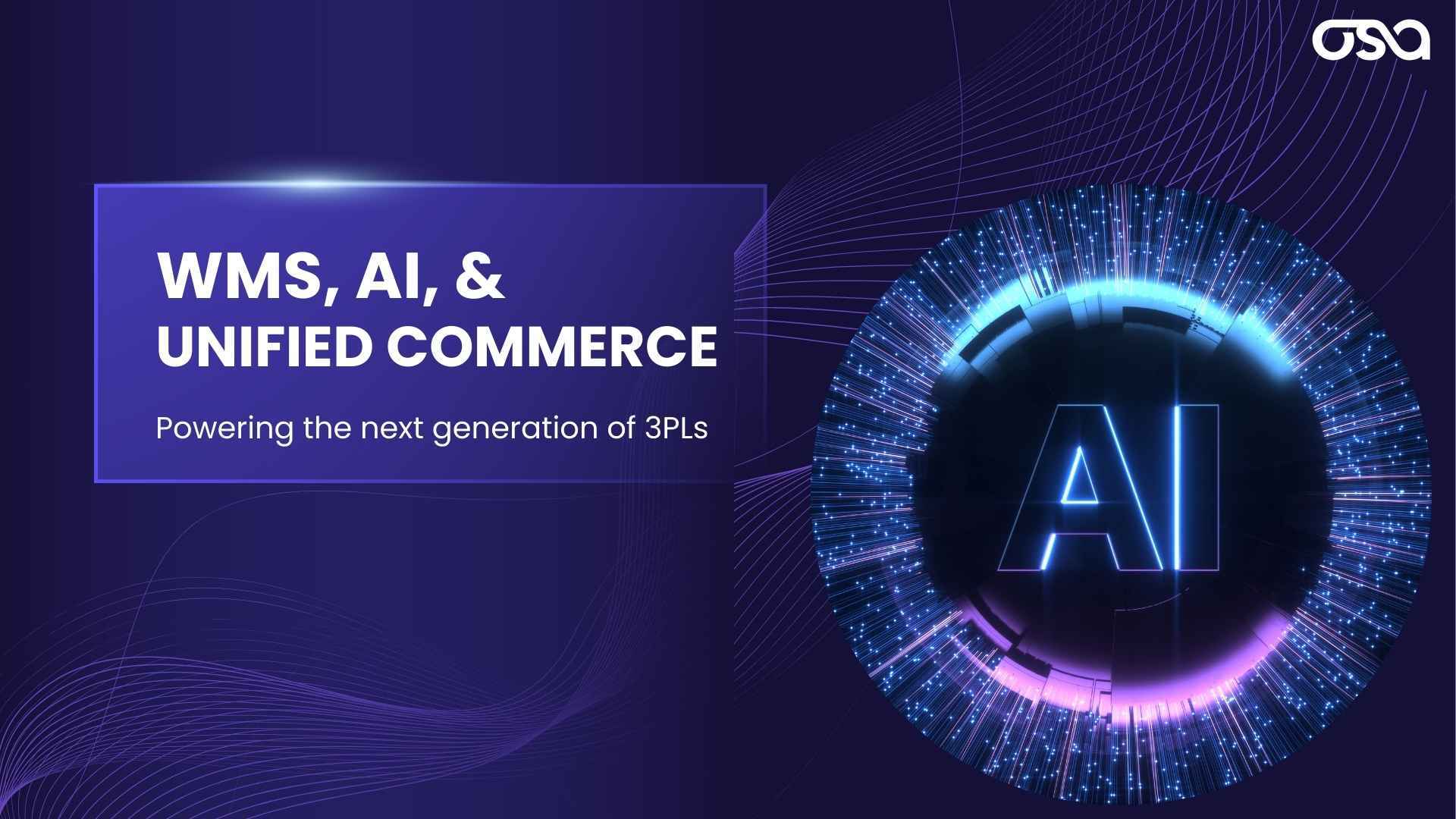
How WMS, AI, and Unified Commerce Are Transforming 3PLs
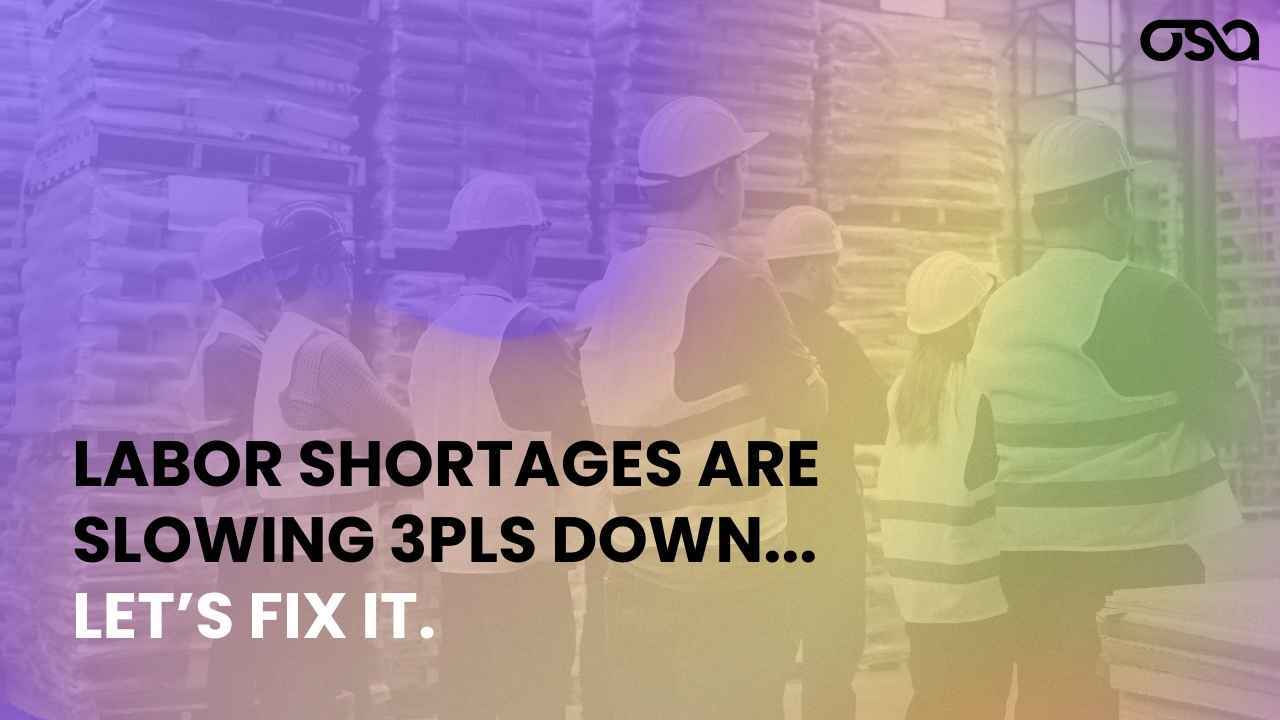
Labor Shortages Are Strangling 3PL Growth — Fix It with AI and Unified Commerce
Objectives of Order Orchestration
Order orchestration systems are designed to manage and streamline the end-to-end order fulfillment process. The primary objectives of these systems can be broadly categorized into optimizing supply chain operations, providing excellent customer experience, reducing costs, and improving accuracy.
Several objectives that contribute to optimizing supply chain operations include:
Optimize Supply Chain Operations
One of the key objectives of an order orchestration system is to optimize supply chain operations. This involves integrating various components of the supply chain, such as inventory management, order processing, and shipping logistics, into a cohesive and efficient workflow. By automating these processes with collaborative technologies, order orchestration systems can ensure that each step in the supply chain is executed seamlessly and promptly. This reduces bottlenecks, enhances communication between departments, and allows for better resource allocation. The result is a more responsive and agile supply chain that can adapt to fluctuations in demand and other external factors.
Provide Excellent Customer Experience
Providing an excellent customer experience is another critical objective of order orchestration systems. In today's competitive e-commerce market, customer satisfaction is paramount. An order orchestration system ensures that customers receive timely updates about their order status, accurate tracking information, and on-time deliveries. By efficiently managing the entire order lifecycle, these systems minimize delays and errors, leading to higher customer satisfaction. Additionally, a well-orchestrated order process can handle returns and exchanges smoothly, further enhancing the customer experience.
Reduce Costs
Reducing operational costs is a significant objective of implementing an order orchestration system. By automating manual processes and optimizing the use of resources, these systems can significantly cut down on labor costs, reduce inventory holding costs, and minimize errors that lead to costly rework or returns. Efficiently managing inventory and ensuring accurate order fulfillment also helps in reducing excess stock and avoiding stockouts, both of which contribute to cost savings.
Improve Accuracy
Improving accuracy in order processing and fulfillment is a fundamental objective of order orchestration systems. These systems leverage automation and real-time data integration to reduce human errors and ensure that orders are processed correctly the first time. Accurate inventory data, order information, and shipping details reduce the likelihood of mistakes, such as shipping the wrong items or misplacing orders. This not only saves costs associated with correcting errors but also enhances customer trust and reliability.
Benefits of Order Orchestration
Optimizing order orchestration offers a variety of benefits that help retailers, brands and their logistics partners enhance the efficiency and effectiveness of the order fulfillment process. Some of these benefits to improve supply chain operations include:
Customizing Routing Logic
One significant benefit of order orchestration is the ability to customize routing logic. This means businesses can tailor the order flow according to specific criteria such as order type, customer priority, or geographic location. By customizing routing logic, companies can ensure that high-priority orders are processed faster, improve overall order turnaround times, and enhance the flexibility and responsiveness of their supply chain operations. This customization helps in meeting diverse customer demands and improving service levels. Add in the power of Artificial Intelligence (AI), and supply chain platforms utilizing order orchestration processes, and adapt in real-time for dynamic routing based on current road or weather conditions.
Defining Order Split Counts
Order orchestration allows businesses to define order split counts, which means dividing a single order into multiple shipments based on factors like product availability, warehouse location, or shipping method. For businesses utilizing fourth party logistics (4PL) services this capability is crucial for optimizing delivery times and reducing shipping costs. For instance, if a particular item is out of stock at one location but available at another, splitting the order can ensure timely fulfillment without waiting for restocks. This also minimizes delays and improves customer satisfaction by ensuring quicker deliveries.
Setting Item-Specific Assignment Logic
Setting item-specific assignment logic is another advantage. This involves assigning specific handling and processing rules to different items based on their characteristics, such as size, weight, or perishability. By doing so, businesses can ensure that each item is processed in the most efficient and appropriate manner. For example, perishable or cold storage goods can be prioritized for faster processing and shipping, while larger items can be assigned to facilities equipped to handle them. This improves the efficiency and accuracy of order fulfillment. These rules can be automated via a WMS for enhanced pick, pack, and ship workflow—not only by product but also by warehouse customers.
Scheduling Location Downtime
Scheduling of location downtime for planned maintenance or operational downtimes at warehouses and distribution centers are accounted for in the order fulfillment process. By integrating downtime schedules, the integrated inventory, order or warehouse management systems can reroute orders to other locations, preventing delays and maintaining a smooth workflow. This proactive approach ensures that disruptions are minimized, and orders continue to be processed and shipped without significant interruptions.
Finding the Best Assignment Locations for Order Items
Another critical benefit is the ability to find the best assignment locations for order items. Order orchestration helps to analyze various factors such as inventory levels, proximity to the customer, and shipping costs to determine the most efficient fulfillment locations. This optimization reduces shipping times and costs, enhances inventory utilization, and improves overall operational efficiency. By strategically assigning orders to the best locations, businesses can achieve faster delivery times and lower operational expenses, leading to increased customer satisfaction and cost savings.
Common Order Orchestration Rules
Order orchestration rules are essential for managing and optimizing the order fulfillment process in complex supply chain environments. These rules help businesses streamline operations, reduce costs, and improve customer satisfaction by ensuring that orders are processed efficiently and accurately. Below, we delve into some common order orchestration rules to ensure efficient order processing and fulfillment.
1. Control Split Shipments to Optimize Order Allocation and Reduce Shipping Costs
Split shipments occur when a single customer order is divided into multiple shipments from different locations. While this approach can expedite delivery by sourcing items from multiple warehouses, it often increases shipping costs and complexity. Controlling split shipments is a crucial order orchestration rule aimed at optimizing order allocation and minimizing these additional costs.
Advantages of Controlling Split Shipments:
-
Cost Reduction
By consolidating items into fewer shipments, businesses can significantly reduce shipping costs. -
Customer Satisfaction
Customers prefer receiving their orders in a single package rather than multiple deliveries, improving their overall shopping experience. -
Efficiency
Reducing the number of shipments simplifies logistics and reduces the workload on fulfillment centers.
Strategies to Control Split Shipments:
-
Inventory Synchronization
Ensure real-time inventory visibility across all locations to allocate orders to warehouses that can fulfill the entire order. -
Proximity Optimization
Assign orders to the nearest fulfillment center with sufficient stock to reduce split shipments. -
Dynamic Allocation Rules
Implement dynamic rules that prioritize single-location fulfillment based on stock levels, order size, and shipping costs. -
Threshold Settings
Set thresholds for acceptable split shipments based on cost-benefit analysis, such as allowing splits only when it leads to significant delivery time reduction without substantial cost increase.
2. Cost-Based Optimization to Allocate Orders Based on Cost Efficiency
Cost-based optimization is a critical rule in order orchestration, focusing on allocating orders to fulfillment centers that can process and ship them most cost-effectively. This approach balances the costs associated with inventory holding, handling, and shipping to maximize overall cost efficiency.
Advantages of Cost-Based Optimization:
-
Cost Efficiency
Minimizes operational and shipping costs by leveraging the most cost-effective fulfillment options. -
Resource Utilization
Optimizes the use of inventory and warehouse resources. -
Competitive Pricing
Allows businesses to offer competitive pricing by controlling fulfillment costs.
Strategies for Cost-Based Optimization:
-
Cost Analysis Models
Develop detailed cost models that account for storage, handling, and shipping expenses at different locations. -
Automated Decision-Making
Utilize automated systems to dynamically evaluate cost factors and allocate orders accordingly. -
Supplier Agreements
Negotiate favorable shipping rates with carriers and consider these rates in the optimization process. -
Multi-Echelon Inventory
Implement multi-echelon inventory strategies to balance stock across multiple levels in the supply chain for cost efficiency.
3. Inventory Life to Date to Prioritize Order Allocation Based on Inventory Availability
Inventory Life to Date (LTD) is a metric used to prioritize order allocation based on the age and turnover rate of inventory. This rule ensures that older stock is utilized first, reducing the risk of obsolescence and spoilage, especially for perishable or time-sensitive products.
Advantages of LTD-Based Allocation:
-
Inventory Turnover
Improves inventory turnover rates by prioritizing older stock. -
Waste Reduction
Minimizes waste and losses due to expired or obsolete products. -
Cost Savings
Reduces costs associated with excess and obsolete inventory.
Strategies for LTD-Based Allocation:
-
FIFO (First In, First Out)
Implement FIFO principles to allocate the oldest inventory first. -
Real-Time Tracking
Use real-time inventory tracking systems to monitor stock age and turnover. -
Automated Allocation Rules
Set up automated rules that prioritize orders to locations with older inventory. -
Stock Rotation Policies
Regularly rotate stock within warehouses to ensure even turnover and utilization.
Assignment Throttling and Thresholds to Control the Rate of Order Assignment
Assignment throttling and thresholds are critical for managing the rate at which orders are assigned to fulfillment centers. These rules prevent overloading any single location, ensuring a balanced distribution of work and maintaining operational efficiency.
Advantages of Assignment Throttling and Thresholds:
-
Operational Balance
Prevents bottlenecks and ensures a smooth flow of orders through the fulfillment process. -
Performance Stability
Maintains consistent performance levels across all fulfillment centers. -
Scalability
Supports scalability by allowing controlled order allocation based on capacity.
Strategies for Assignment Throttling and Thresholds:
-
Capacity Monitoring
Continuously monitor the capacity and workload of each fulfillment center. -
Dynamic Throttling
Implement dynamic throttling rules that adjust based on real-time capacity and order volume. -
Threshold Settings
Define clear thresholds for order assignment, such as maximum orders per hour or day for each location. -
Load Balancing
Use load balancing algorithms to distribute orders evenly across all available locations.
Item-Specific Assignment to Allocate Orders Based on Specific Item Characteristics
Item-specific assignment involves allocating orders based on the unique characteristics of the items being ordered, such as size, weight, perishability, or handling requirements. This rule ensures that each item is processed in the most appropriate and efficient manner.
Advantages of Item-Specific Assignment:
-
Efficiency
Ensures items are processed by facilities best equipped to handle their specific characteristics. -
Accuracy
Reduces errors by matching items to the right fulfillment locations and handling processes. -
Specialization
Leverages specialized capabilities of different fulfillment centers.
Strategies for Item-Specific Assignment:
-
Categorization
Categorize inventory based on characteristics such as size, weight, and perishability. -
Specialized Fulfillment Centers
Designate specific fulfillment centers for handling certain types of items. -
Automated Matching
Use automated systems to match orders with the most suitable fulfillment centers based on item characteristics. -
Handling Protocols
Develop and implement handling protocols for different item categories to ensure consistency and accuracy.
Geographic Proximity to Allocate Orders to Locations That Are Geographically Closer to the Customer
Geographic proximity is a fundamental rule in order orchestration, aiming to allocate orders to fulfillment centers that are geographically closer to the customer. This approach reduces shipping times and costs, enhancing customer satisfaction.
Advantages of Geographic Proximity:
-
Faster Delivery
Shortens delivery times by minimizing the distance between fulfillment centers and customers. -
Cost Reduction
Reduces shipping costs by selecting the nearest fulfillment centers. -
Environmental Impact
Lowers carbon footprint by decreasing the distance goods need to travel.
Strategies for Geographic Proximity:
-
Regional Warehousing
Establish regional warehouses to ensure broad geographic coverage and proximity to major customer bases. -
Proximity Algorithms
Use algorithms to calculate the nearest fulfillment centers based on customer location. -
Real-Time Location Data
Integrate real-time location data to dynamically adjust order allocation based on geographic proximity. -
Route Optimization
Implement route optimization software to further enhance delivery efficiency and reduce transit times.
Steps Involved in Order Orchestration Process
The order orchestration process is a critical aspect of efficient order fulfillment, encompassing several key steps to ensure that customer orders are handled smoothly and accurately from start to finish. Here are the essential steps involved:
Order Creation:
The process begins with order creation, where customer orders are captured and recorded. In most cases, this involves OMS or DOM platforms. This step involves inputting order details, such as product information, quantities, customer details, and payment information. Accurate data entry at this stage is crucial for preventing errors and ensuring that subsequent steps proceed without issues.
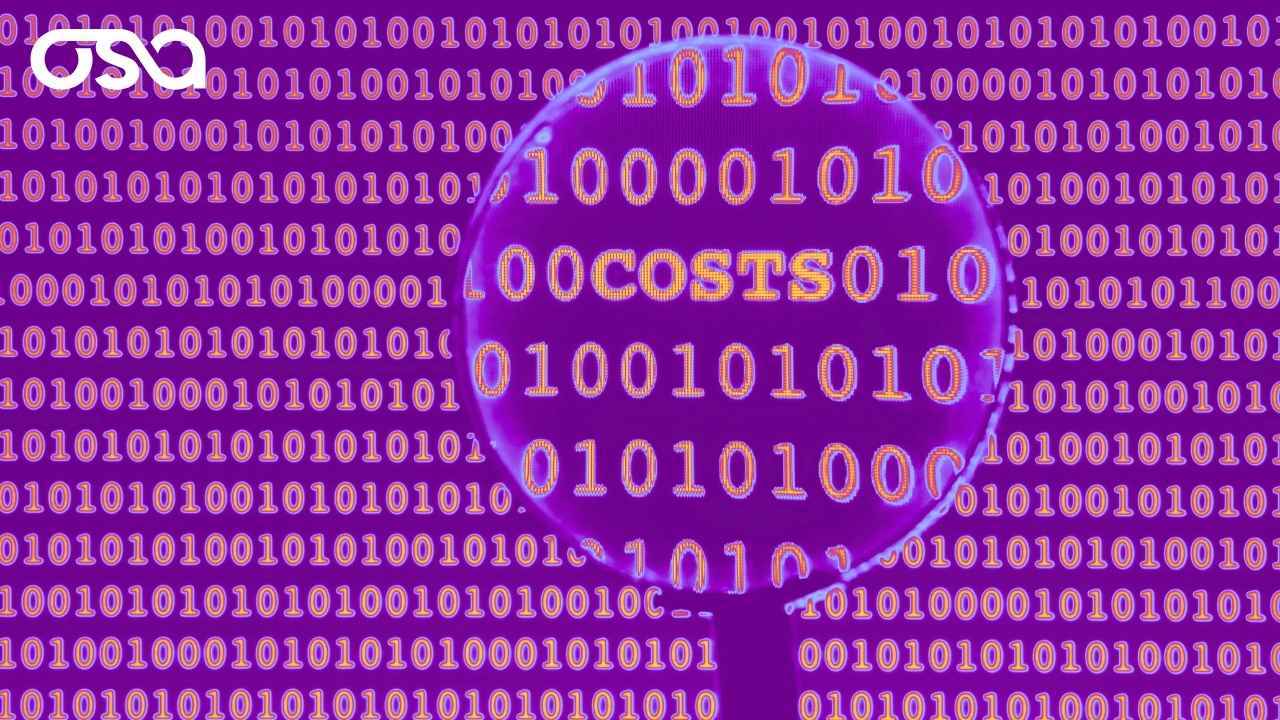
How to Reduce Logistics Costs with Supply Chain Integrations
Order Fulfillment:
Once an order is created, businesses use supply chain technology platforms to process and allocate orders based on predefined rules, such as inventory availability, cost efficiency, and geographic proximity. This step includes picking, packing, and preparing the order for shipment. Automated systems, artificial intelligence (AI), and real-time data integration play a vital role in optimizing order fulfillment, ensuring that orders are processed quickly and accurately.
Order Shipping:
After fulfillment, the order is packaged and shipped to the customer. This step involves selecting the appropriate shipping method, generating shipping labels, and coordinating with logistics providers. Efficient shipping processes and rate shopping opportunities can help minimize delivery times, reduce costs, and enhance customer satisfaction.
Inventory Adjustment:
As orders are fulfilled and shipped, inventory levels must be updated to reflect the changes. This step involves real-time adjustments to inventory records, ensuring that stock levels are accurate and available for future orders. Effective inventory management, with the help of AI, helps prevent stockouts and overstock situations.
Return Processing:
Handling customer returns is an integral part of the order orchestration process. This step includes receiving returned items, inspecting them, processing refunds or replacements, and updating inventory records accordingly. A streamlined return process improves customer trust and satisfaction.
Order Settlement:
The final step in the order orchestration process is order settlement, which involves completing the financial aspects of the order. This includes updating financial records, processing payments, and reconciling accounts. Ensuring accurate and timely order settlement is crucial for maintaining financial integrity and customer trust.
By following these steps, supply chain businesses can ensure a seamless and efficient order orchestration process, leading to improved operational efficiency, reduced costs, and enhanced customer satisfaction.
Conclusion
Mastering order orchestration is essential for enhancing supply chain efficiency and optimizing operations in the competitive landscape of e-commerce and omnichannel retailing. By implementing the strategies and best practices outlined in this guide, businesses can streamline their order fulfillment processes, reduce operational costs, and significantly improve customer satisfaction.
Order orchestration goes beyond traditional order management by integrating and automating various steps in the fulfillment process. This includes creating customer orders, processing and allocating them based on sophisticated rules, shipping, and handling returns efficiently. Each step in the order orchestration process is crucial for maintaining the smooth flow of operations and ensuring that customers receive their orders accurately and on time.
Key differences between order orchestration and order management highlight the importance of a seamless and automated fulfillment process. Order management focuses on capturing and tracking orders, while order orchestration optimizes these processes through real-time data integration and automation. This optimization leads to faster order fulfillment, improved accuracy, and better resource utilization.
Order orchestration is a critical component of modern supply chain management. By leveraging advanced technologies, real-time data integration, and automated systems, businesses can enhance operational efficiency, reduce costs, and deliver superior customer experiences. As technology continues to evolve, staying ahead of emerging trends and continuously optimizing order orchestration processes will be key to maintaining a competitive edge in the dynamic world of e-commerce and supply chain operations.