8 min read
The Order Fulfillment Process: Definition, Steps, & Benefits for Supply Chain Management
Katie Dalrymple
:
June 3, 2024
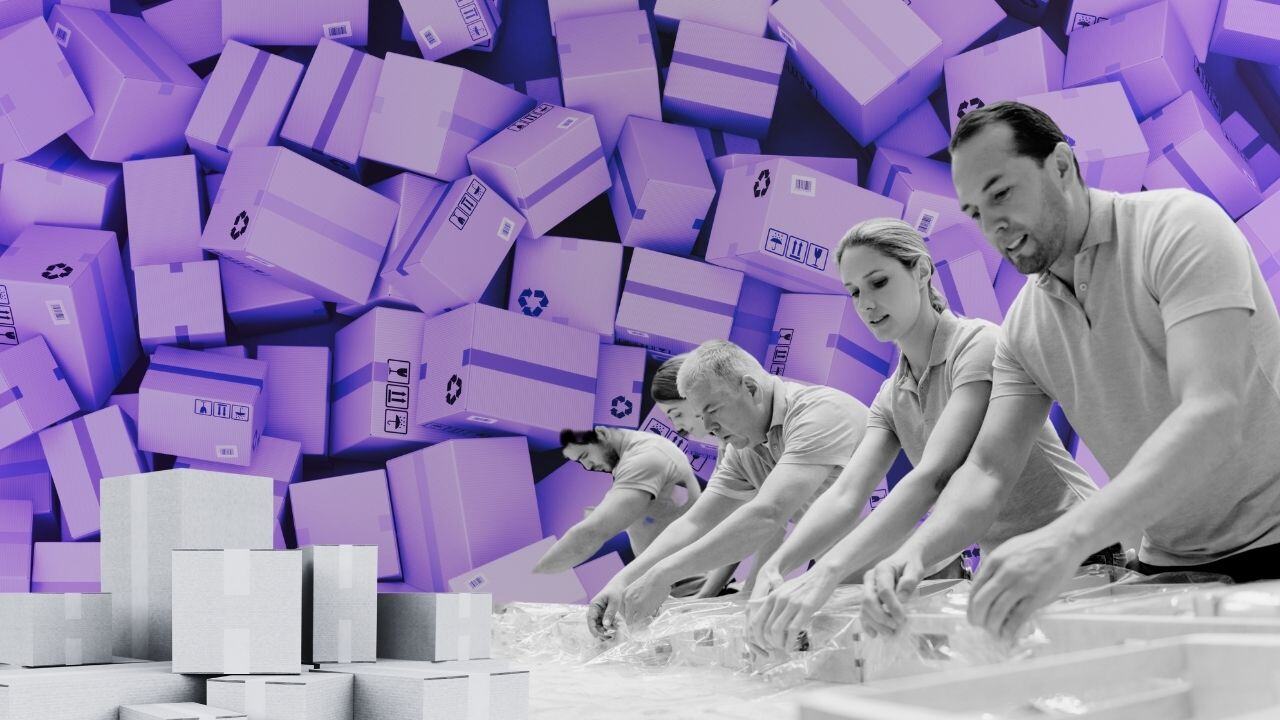
What is the Order Fulfillment Process?
Order fulfillment is a comprehensive process that begins when an order is placed by a customer or a sale is made and concludes when the customer receives the ordered product. This intricate process is essential to supply chain management and involves several critical steps to ensure timely and accurate delivery. The success of the order fulfillment process often depends on the involvement of third-party logistics companies (3PLs) or fulfillment centers, which manage and streamline the various stages of fulfillment. There are four main kinds of order fulfillment processes in-house fulfillment, outsourced fulfillment, drop shipping, and hybrid fulfillment.
Fulfillment services play a pivotal role in managing and processing orders for businesses. These services provide not only a storage location for inventory but also the necessary personnel to handle and dispatch orders efficiently. One key aspect of fulfillment services is business-to-business (B2B) fulfillment, which involves shipping bulk supplies to businesses. Companies utilizing B2B fulfillment often purchase products in advance, allowing them to maintain stock without the need for daily purchases. Additionally, they may provide merchandise to other companies for resale.
Fulfillment services streamline the complex logistics of product handling and shipping for business owners. They start by receiving, inspecting, and inventorying products, followed by secure storage in climate-controlled warehouses. These services include order management, where personnel pick, pack, and ship products, notifying the customer of shipment. They also handle returns efficiently and use real-time inventory technology to provide up-to-date stock data, ensuring accuracy and informed decision-making for businesses.
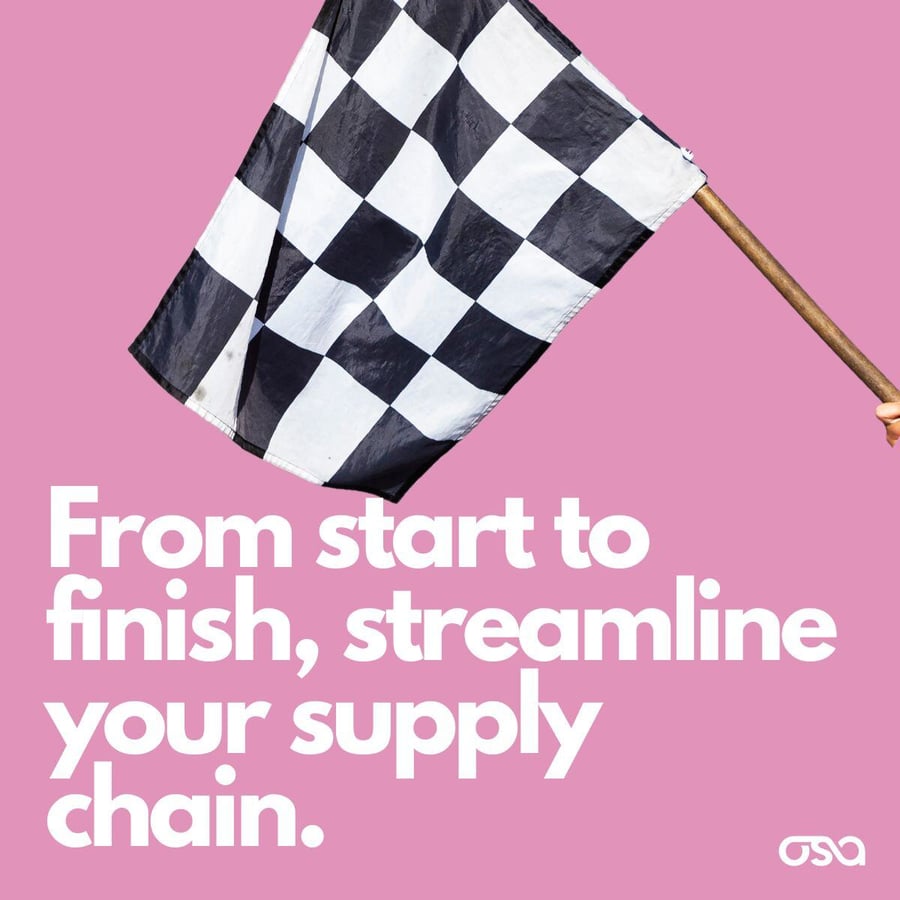
In essence, order fulfillment is a critical process in supply chain management that encompasses the complete journey from when an order is placed until it is delivered to the customer. By efficiently managing the steps from receiving inventory to delivering the product to the customer, and by leveraging the capabilities of 3PLs and fulfillment centers, companies can ensure a seamless and satisfying customer experience. This streamlined process enables businesses to focus on their core operations without worrying about logistical challenges.
What are the Order Fulfillment Process Steps?
The core function of fulfillment services lies in managing the logistical intricacies that can overwhelm business owners who need to ensure their products are properly handled and shipped. These services begin by accepting the arrival of products, inspecting the inventory for any damage, and conducting a quantity count. A report detailing the inventory is then forwarded to the business owner.
Once the inventory is received and inspected, it is stored in a designated area within the warehouse. This storage environment is protected, climate-controlled, and equipped with sprinkler systems to ensure the safety and preservation of the products. Dedicated personnel maintain the warehouse, ensuring cleanliness, safety, and adherence to all necessary protocols.
Order management is a key component of fulfillment services. Upon receiving an order, the personnel pick, pack, and ship the products to the business that placed the order. The business customer is then notified of the shipment, keeping them informed throughout the process.
Additionally, fulfillment services manage returns efficiently. Any issues regarding returns are handled by the personnel, ensuring that the process is smooth and hassle-free for the business customer. To maintain accuracy and transparency, real-time inventory technology is employed. This technology provides up-to-date inventory data, allowing businesses to monitor their stock levels and make informed decisions. Here is a breakdown of the order fulfillment process steps that most strategies follow:
Receiving Inventory
The process starts with receiving products from suppliers or manufacturers. This step involves unloading shipments, checking the received items against purchase orders, inspecting for damage, and storing the inventory in the warehouse. Efficient inventory management systems are essential to keep track of stock levels and ensure accurate order fulfillment.
Storing Inventory
When inventory is organized and stored in designated locations within the warehouse. Effective organization is crucial, as it significantly enhances both speed and efficiency in handling orders.
Processing Inventory
Once an order is placed, it enters the processing stage. This involves verifying order details, checking inventory availability, and ensuring that payment has been received. Order processing systems, often integrated with e-commerce platforms, automate much of this work, reducing errors and speeding up the workflow.
Picking Inventory
In this step, items listed in the customer’s order are picked from the warehouse shelves. The picking process can vary in complexity depending on the warehouse setup and the type of products. Efficient picking strategies, such as batch picking or zone picking, are employed to minimize time and labor costs while ensuring accuracy.
Packing Inventory
After picking, the items are moved to the packing station. Here, the products are securely packed in appropriate packaging materials to prevent damage during transit. The packaging also includes necessary documentation, such as invoices and return labels, and proper labeling with the customer’s shipping information.
Shipping Inventory
The final step in the order fulfillment process is shipping the packed order to the customer. This involves selecting a shipping carrier, generating shipping labels, and arranging for pickup or delivery. Advanced logistics solutions help track shipments in real-time and provide customers with updates on the status of their orders.

What are the Benefits of the Order Fulfillment Process?
An effective order fulfillment system yields numerous benefits throughout the supply chain. It fosters competitiveness by facilitating quicker order processing, reducing lead times, and extending market reach, empowering businesses to surpass customer expectations while maintaining a competitive edge. It can contribute to cost reduction through optimized inventory management, decreased holding costs, and streamlined operational workflows, resulting in lower shipping and operational expenses. Moreover, an order fulfillment strategies enhance customer satisfaction by ensuring accurate, swift, and efficient handling of orders, leading to enhanced customer retention rates and positive brand perception. With timely deliveries and shipments, the advantages are significant. Essentially, a well-executed order fulfillment process enhances operational efficiency, customer satisfaction, and competitiveness, positioning businesses for sustainable and scalable growth and success.
Gaining a Competitive Advantage for Your Business
Efficient and perfect order fulfillment processes contribute significantly to gaining a competitive advantage in the market. From order fulfillment for traditional retail, to order fulfillment for ecommerce, to order fulfillment for omnichannel strategies there are many opportunities for competition. By streamlining operations from order placement to delivery, businesses can enhance their overall efficiency, reduce costs, and improve customer satisfaction. A well-organized fulfillment system allows companies to fulfill orders quickly and accurately, leading to faster delivery times and higher customer retention rates. Moreover, by optimizing inventory management and reducing order processing times, businesses can stay ahead of competitors by offering faster and more reliable service.
Providing Deliveries that Meet Customer Expectations
Order fulfillment strategies play a crucial role in meeting customer expectations for timely and accurate deliveries. By efficiently managing inventory, processing orders promptly, and optimizing picking and packing procedures, businesses can ensure that customers receive their orders on time and in good condition. Meeting or exceeding customer expectations fosters loyalty and positive brand perception, leading to increased customer satisfaction and repeat business. Additionally, effective order fulfillment in supply chain management enhances the overall shopping experience, reinforcing trust and confidence in the brand.
Ensuring On-time Shipments and Deliveries
Timely shipments and deliveries are essential for maintaining a competitive edge and meeting customer demands. Efficient order fulfillment processes enable businesses to manage inventory levels effectively, minimize stockouts, and fulfill orders promptly. By implementing streamlined workflows, automated order management systems, and real-time inventory tracking, companies can ensure that orders are processed, packed, and shipped accurately and efficiently. Meeting delivery deadlines consistently not only enhances customer satisfaction but also helps to build a reputation for reliability and professionalism, setting businesses apart from competitors.
What are the Best Practices of the Order Fulfillment Process in Supply Chain Management?
In supply chain management, effective order fulfillment processes are essential for meeting customer demands efficiently while optimizing operational performance. Several best practices contribute to perfect order fulfillment such as automation, inventory optimization, streamlined communication, continuous improvement, tailoring the strategies to your needs, and the integration of technology. By adhering to these best practices, supply chain businesses can enhance customer satisfaction, reduce operational costs, and maintain a competitive edge in the market.
Clearly Communicate
Effective communication is paramount in order fulfillment supply chain management businesses. Clear communication channels between different stakeholders, including suppliers, manufacturers, distributors, and customers, ensure smooth operations and minimize errors. Businesses should establish transparent communication protocols, detailing order specifications, delivery schedules, and any potential disruptions. Utilizing advanced communication tools and platforms can facilitate real-time updates and notifications, keeping all parties informed throughout the process.
Apply New Technology Systems
Embracing new technology systems is crucial for optimizing an order fulfillment system. Implementing advanced software solutions such as warehouse management systems (WMS), inventory tracking software, and automated order management platforms can streamline operations, enhance accuracy, and improve efficiency. These systems enable real-time inventory visibility, automated order processing, and predictive analytics, empowering businesses to make data-driven decisions and adapt to changing market demands swiftly. Investing in technology ensures competitiveness and scalability in the increasingly digitalized supply chain landscape.
Choose the Best Process for Your Company
Every supply chain business is unique, and selecting the most suitable order fulfillment process is essential for success. Companies should assess their specific needs, considering factors such as order volume, product complexity, and customer expectations. Whether employing a traditional warehouse model, utilizing 3PLs, or adopting dropshipping strategies, the chosen process should align with the company's goals, capabilities, and resources. Flexibility and adaptability are key, allowing businesses to tailor their fulfillment approach as they grow and evolve.
What is the Importance of Order Fulfillment in Supply Chain Management?
3PLs, 4PLs, and fulfillment centers play a crucial role in modern order fulfillment strategies. They offer specialized services and infrastructure that allow businesses to handle large volumes of orders efficiently. By outsourcing to 3PLs and other logistics businesses, companies can benefit from:
Reduction in Operational Costs
Efficient order fulfillment streamlines processes, reducing labor and overhead costs. Automation and optimization minimize errors, leading to cost savings.
Lower Your Shipping Costs
By leveraging the infrastructure and negotiated shipping rates of 3PLs, businesses can often reduce shipping costs and improve profit margins. Optimized order fulfillment also reduces order processing time, enabling faster shipping and potentially lower shipping costs. Efficient packaging practices also contribute to reducing shipping expenses.
Globally Expand Your Customer Base
3PLs offer scalable solutions that can adapt to fluctuating order volumes, especially during peak seasons or promotional events. A streamlined order fulfillment system enables businesses to fulfill orders across borders and selling channels efficiently, facilitating global expansion. Timely delivery enhances customer satisfaction, fostering loyalty and encouraging repeat purchases
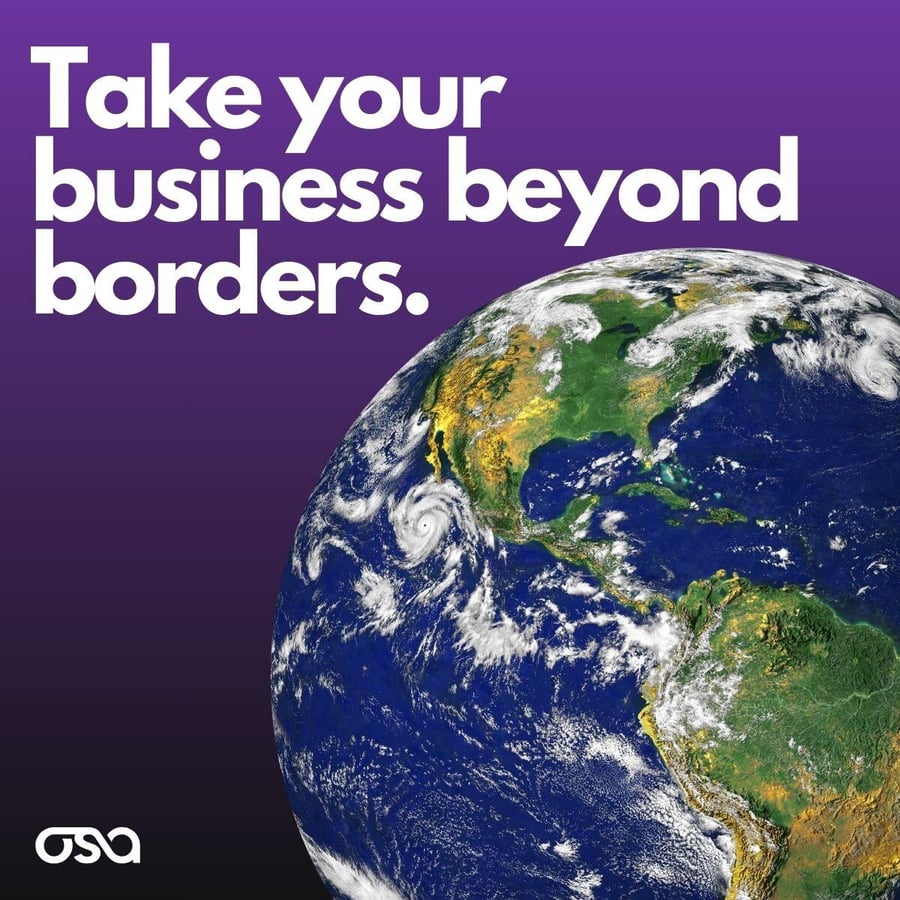
Enhance Your Customers' Experience
Efficient order fulfillment ensures timely delivery and accurate order processing, leading to improved customer satisfaction. Clear communication channels and reliable shipping options contribute to a positive customer experience.
Focus on Selling Product
By automating order processing and inventory management, businesses can focus more resources on sales and marketing efforts. Efficient order fulfillment allows companies to concentrate on expanding their product offerings and reaching new markets.
Overall, prioritizing order fulfillment processes in supply chain management contributes to cost reduction, improved customer service, and business growth opportunities.
What are the Challenges and Strategies in Order Fulfillment Processes?
Despite its importance, order fulfillment can present several challenges, such as managing high order volumes, ensuring accurate inventory levels, and meeting customer delivery expectations. To address these challenges, businesses can adopt various strategies, including:
Automation
Implementing automated systems for order processing, inventory management, and picking can significantly enhance efficiency and accuracy.
Demand Forecasting
Using data analytics to predict demand helps in maintaining optimal inventory levels and reduces the risk of stockouts or overstocking.
Customer Communication
Providing customers with timely updates on their order status and delivery can improve satisfaction and reduce inquiries or complaints.
Returns Management
Developing a streamlined returns process ensures that returned products are quickly restocked and made available for resale, enhancing overall inventory turnover.
Technology Integration into Your Order Fulfillment Process
Advanced 3PLs use cutting-edge technology, such as warehouse management systems (WMS) and transportation management systems (TMS), to optimize the fulfillment process and provide real-time visibility into order status and inventory levels.
Artificial Intelligence (AI) has revolutionized order fulfillment by introducing unprecedented levels of efficiency and accuracy. By leveraging AI algorithms, businesses can eliminate the guesswork traditionally involved in order fulfillment. Here’s how AI enhances each step of the order fulfillment process:
Predicting Demand Patterns
AI systems analyze historical data to forecast demand trends with high precision. This predictive capability allows warehouses to maintain optimal inventory levels, ensuring that popular items are always in stock while reducing excess inventory of slower-moving products.
Optimizing Picking Routes
AI-driven algorithms can design the most efficient picking routes within the warehouse. By considering variables such as product location, order frequency, and the layout of the warehouse, AI minimizes the travel time for pickers, significantly speeding up the order-picking process. This optimization not only reduces lead times but also enhances overall productivity.
Enhancing Inventory Management
AI tools help maintain accurate inventory records by continuously monitoring stock levels and automating the reordering process. This reduces the likelihood of stockouts and overstock situations, ensuring that inventory is managed efficiently and costs are minimized.
Automating Mundane Tasks
AI can take over repetitive and mundane tasks such as data entry and routine checks, freeing up human workers to focus on more complex and value-added activities. This not only improves employee productivity but also reduces the chances of human error.
Improving Order Accuracy
AI systems ensure that orders are processed accurately by automating order verification and matching processes. This reduces the incidence of errors such as shipping the wrong items or incorrect quantities, leading to higher customer satisfaction and fewer returns.
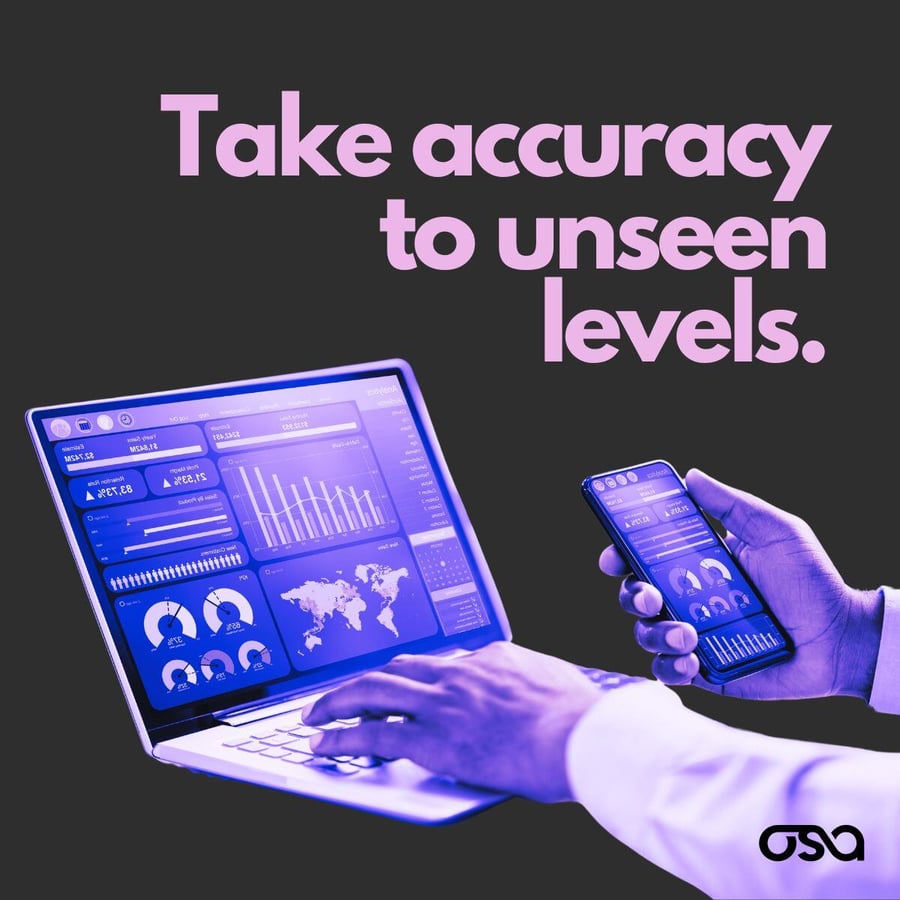
Boosting Customer Satisfaction
By streamlining processes and reducing lead times, AI helps ensure that customers receive their orders faster and more reliably. The ability to predict demand accurately and manage inventory effectively means that customers are less likely to encounter out-of-stock items, enhancing their overall shopping experience.
AI has the power to transform order fulfillment strategies from a complex and error-prone process into a streamlined and efficient operation. By leveraging the power of AI, businesses can achieve new standards of excellence in order fulfillment, ensuring that customers receive their orders accurately and promptly. AI is not just enhancing the process; it is setting a new benchmark for what is possible in supply chain management.
Conclusion
Order fulfillment, vital in supply chain management, spans from order placement to delivery. Businesses must select the right method, be it in-house, outsourced, dropshipping, or hybrid, to meet both company and customer needs. Third-party logistics companies (3PLs) and fulfillment centers play a crucial role in managing and streamlining fulfillment stages by providing storage, personnel, and efficient order processing, including B2B fulfillment. These services streamline product handling, storage, order management, and shipping, ensuring accuracy and efficient return handling. By optimizing these processes and utilizing 3PLs and fulfillment centers, businesses can focus on core operations, ensuring a seamless customer experience and profitability.
Discover more about how Osa Commerce can meet your own order fulfillment needs!