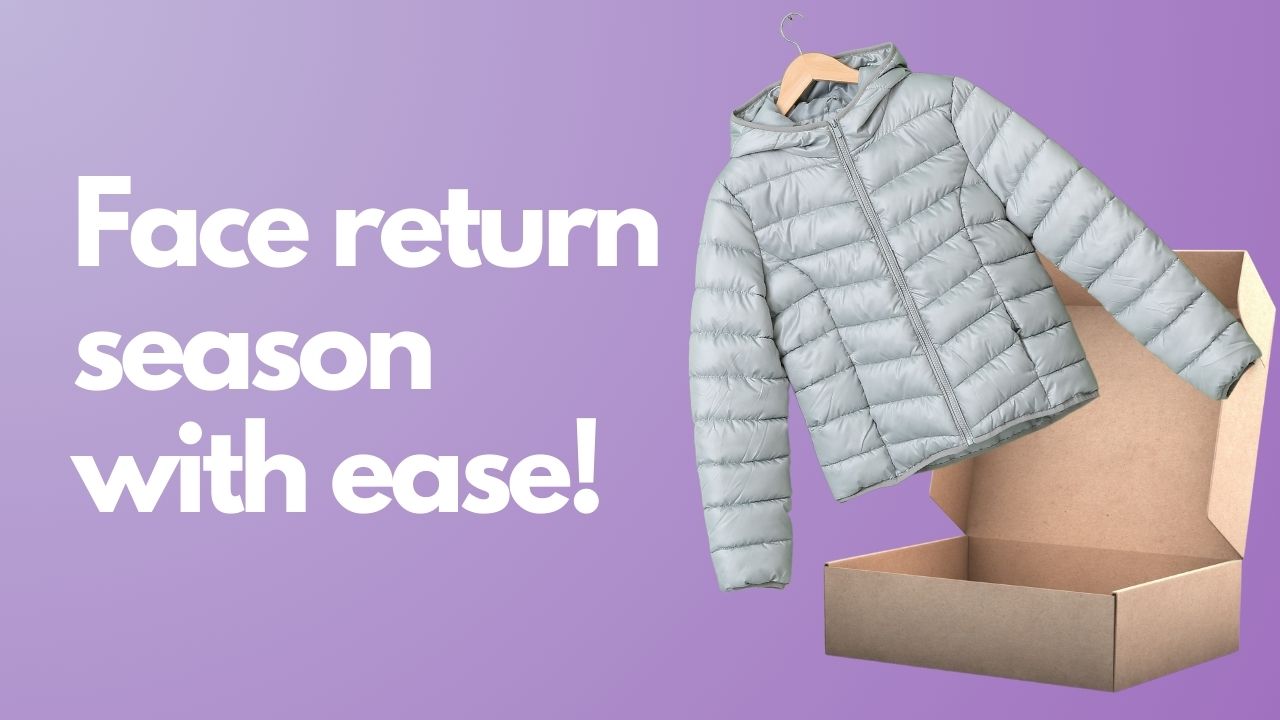
Still struggling with holiday returns?
Not only are they time consuming, they can be costly. Learn how technology can help your business improve forecasting, reporting, operations, and save you money.
Return season can be a challenging time for any business, especially around the holiday season when return policies can be a little muddled. Many retailers have complicated processes or insufficient data. Some have challenges with sustainability or green promises. Others cite numerous issues with fraud. Unfortunately, there are companies who struggle with all of these issues. However, with the right technology, supply chain businesses can mitigate the impact of returns and, in some cases, prevent them altogether.
Despite their expense, returns are commonplace in e-commerce, with an average return rate of 17%, equating to $816 billion in lost sales. Retailers typically spend $26.50 to process $100 worth of returned products, highlighting the financial implications of return processes.
.jpg?width=1200&height=1200&name=images%20ideas%20(16).jpg)
The importance of implementing and adopting supply chain technology that can revolutionize your returns process is clutch for not only your bottom line—but to also improve your overall customer experience. As a supply chain technology partner to retailers, brands, and 3PLs, we understand first-hand how reduced return rates directly enhance customer satisfaction. Learn how the right supply chain technology utilizing artificial intelligence (AI) can revolutionize the way businesses cope with return season:
AI-Based Inventory Forecasting
Demand and lead times for inventory can be impacted by the latest trends, seasonality, or even rapid growth. Historical data can be a great help when looking to get ahead of the game. Combing through and applying endless amounts of data can be extremely time consuming. AI can help alleviate the manual labor associated with predictive analytics. Even better, AI can help project recommendations and decision support for c-level executives.
Utilizing AI for inventory forecasting enables businesses to accurately predict demand and ensure optimal inventory levels. Inaccurate demand forecasts result in missed revenue opportunities for nearly half of surveyed companies. By analyzing historical data and market trends, AI algorithms can forecast demand with precision, reducing the likelihood of overstock or stock outs that often lead to returns.
.jpg?width=1200&height=2000&name=images%20ideas%20(Infographic).jpg)
Trend Analysis with AI
The ability to identify challenges and industry turning points is often a struggle without access to historical data. But with AI, businesses can use algorithms to gain massive insights.AI-powered trend analysis allows companies to stay ahead of consumer preferences and anticipate future demand. By monitoring social media and other sources, AI can identify emerging trends, enabling businesses to adjust their inventory accordingly and minimize returns resulting from outdated or unpopular products.
Demand varies significantly on a monthly and daily basis, often influenced by social media platforms like TikTok, which can rapidly propel products to viral status. This sudden surge in sales can lead to stockouts, with retailers spending approximately $1 trillion annually to address these issues.
Real-Time Inventory Monitoring
Monitoring inventory is a continuous process. Technology is a requirement for any business looking to automate this process, reduce errors, and improve customer satisfaction.
Order management technology is one of the best ways to gain real-time visibility into inventory levels across multiple locations, ensuring businesses are always informed about current stock levels. This transparency enables proactive decision-making, such as reallocating inventory to meet demand spikes in specific regions, reducing the likelihood of stockouts and associated returns.
Efficiency in Supply Chain Operations
Inefficiencies caused by lack of data around excessive transportation costs, operational errors, or delivery decisions can cause not only inventory overload but just a lack of visibility across the supply chain.
Streamlining supply chain processes through technology enhances efficiency and reduces errors that can lead to returns. From procurement to last mile, automation of tasks like order processing and fulfillment minimizes delays and inaccuracies, ensuring customers receive their orders promptly and accurately, thus decreasing return rates.
.jpg?width=1200&height=1200&name=images%20ideas%20(14).jpg)
Maintaining High Quality and Reputation
Safeguarding your reputation is paramount in this competitive market —which replies purely on your ability to make good on customer promises. Technology plays a very important role in offering businesses the insights needed to ensure consistent quality.
Unified commerce enables businesses to monitor product quality throughout the supply chain, end-to-end visibility. Implementing quality control measures and tracking systems ensures that only high-quality products reach customers, reducing the likelihood of returns due to defects or damage during fulfillment.
Enhancing the Customer Experience
As mentioned, unified commerce is a great way to boost a reputation. When used as a supply chain platform, it helps to create a seamless shopping experience from end-to-end.
Clear communication and user-friendly interfaces improve the overall customer experience, reducing confusion and frustration that may lead to returns. Providing accurate product measurements, detailed descriptions, and easy return processes instill confidence in customers, fostering loyalty and reducing return rates.
We see the sheer level of importance in the customer experience (CX) with 85% of online shoppers stating that a negative delivery experience would deter them from future purchases with the same company. Additionally, over 90% of consumers anticipate receiving their purchases within two to three days, making a seamless supply chain the utmost importance.
.jpg?width=1200&height=1200&name=images%20ideas%20(15).jpg)
Effective Order Management Systems
Errors and delays are just the beginning without a properly integrated order management system. Customer complaints, inventory, and, yes, high return rates are some other common challenges.
Investing in robust order management systems ensures smooth order processing and fulfillment, reducing errors and delays. Centralizing order data and automating order routing minimizes the risk of miscommunication and ensures orders are fulfilled accurately and efficiently.
Integrating data from order processing systems, shopping carts, and marketplaces also ensures is synced in real-time across the entire supply chain to ensure out of stocks, poor reporting, and inaccurate order information is a thing of the past.
Cost-Effective Supply Chain
On average, supply chain disruptions lead to a staggering 107% drop in profitability, emphasizing the critical need for efficient supply chain management and risk mitigation strategies.
Implementing cost-effective supply chain strategies, such as optimizing transportation routes and reducing excess inventory, minimizes the financial impact of returns. By reducing unnecessary expenses associated with returns, businesses can improve their bottom line and allocate resources more efficiently.
These strategies are all made possible by the Osa Commerce Collaborative Visibility Platform, a one stop shop towards creating a unified and efficient supply chain. From order management to fulfillment to integration management the Collaborative Visibility Platform provides the ideal logistics solutions to increasing visibility, connectivity, and resilience.
.jpg?width=1200&height=1200&name=images%20ideas%20(13).jpg)
Reduce Returns with AI
Technology plays a crucial role in helping businesses cope with the return season by reducing return rates, improving efficiency, and enhancing customer satisfaction. By leveraging AI-driven forecasting, real-time inventory monitoring, and streamlined supply chain operations, companies can minimize the impact of returns and maintain a competitive edge in today’s dynamic market landscape.
Don’t wait til tomorrow to level up your supply chain technology! No need to spend next return season stressed, book a demo today!