6 min read
The Future of Omnichannel Fulfillment with Next-Gen WMS Solutions
Katie Dalrymple
:
April 30, 2024
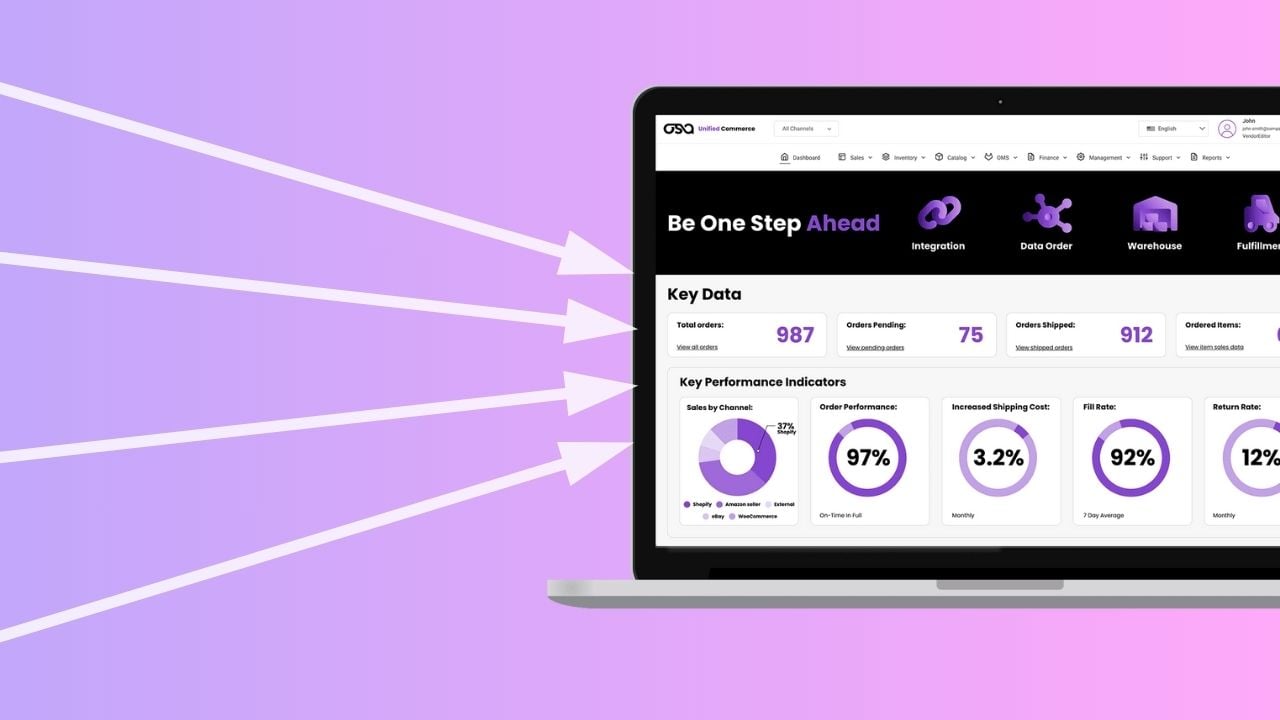
Creating a successful supply chain has never been so important—especially for Third Party Logistics (3PL) warehouses. This year is poised to have yet another impressive market projection of $1.3tn USD, making it the absolute most important time to get processes and systems in order. In addition, evolving consumer demands and technological innovations increase the need for businesses to require seamless integrations across various channels to offer complete supply chain visibility.
So, what’s in store for the next generation of warehouse management systems (WMS) and supply chain technology solutions?
In a word: Resiliency.
One of the most important aspects of a successful supply chain is the ability to adapt and respond effectively to unexpected challenges. Supply chain resiliency has been on full display since the impact of the COVID-19 pandemic. However, the increase in online shopping has boosted demand for 3PL services and created a stronger market showcasing a 49% revenue increase from 2020.
With these market projections, it’s time to buckle in for the global 3PL market to grow due to rising e-commerce and international trade—all a result of the demand from companies and consumers for efficient logistics. In the North American 3PL market, we are witnessing the importance of catering to e-commerce needs in a cost-effective and efficient manner making omnichannel fulfillment imperative to the growth and survival of 3PL businesses.
Today’s most successful supply chain must consider that omnichannel fulfillment is the future. The integration of omnichannel fulfillment with advanced Warehouse Management System (WMS) solutions is becoming increasingly vital to elevate supply chains to grow alongside this market projection. Let’s take a look at the key aspects shaping the future of supply chains and this next-gen of omnichannel fulfillment and warehouse technology.
Table of Contents
What is Omnichannel Fulfillment?
How does a WMS improve Omnichannel Fulfillment?
Why 3PLs need Warehouse Management System (WMS) Automation
Automated vs. Manual Supply Chain Operations
What is the future of supply chains?
How to seamlessly integrate Omnichannel Fulfillment with a Warehouse Management System (WMS)
What is Omnichannel Fulfillment?
Omnichannel fulfillment streamlines integrated sales channels for a unified and seamless customer experience—from order to delivery. The most successful omnichannel fulfillment strategies consolidate and optimize operational processes including picking, packing, and shipping orders sold from a variety of marketplaces, e-commerce, online shopping carts, brick and mortar stores, or wholesale.
Retailers or brands using 3PL warehouses can use omnichannel fulfillment to handle customer orders by tapping into inventory from any sales channel or location for additional flexibility and complete visibility.
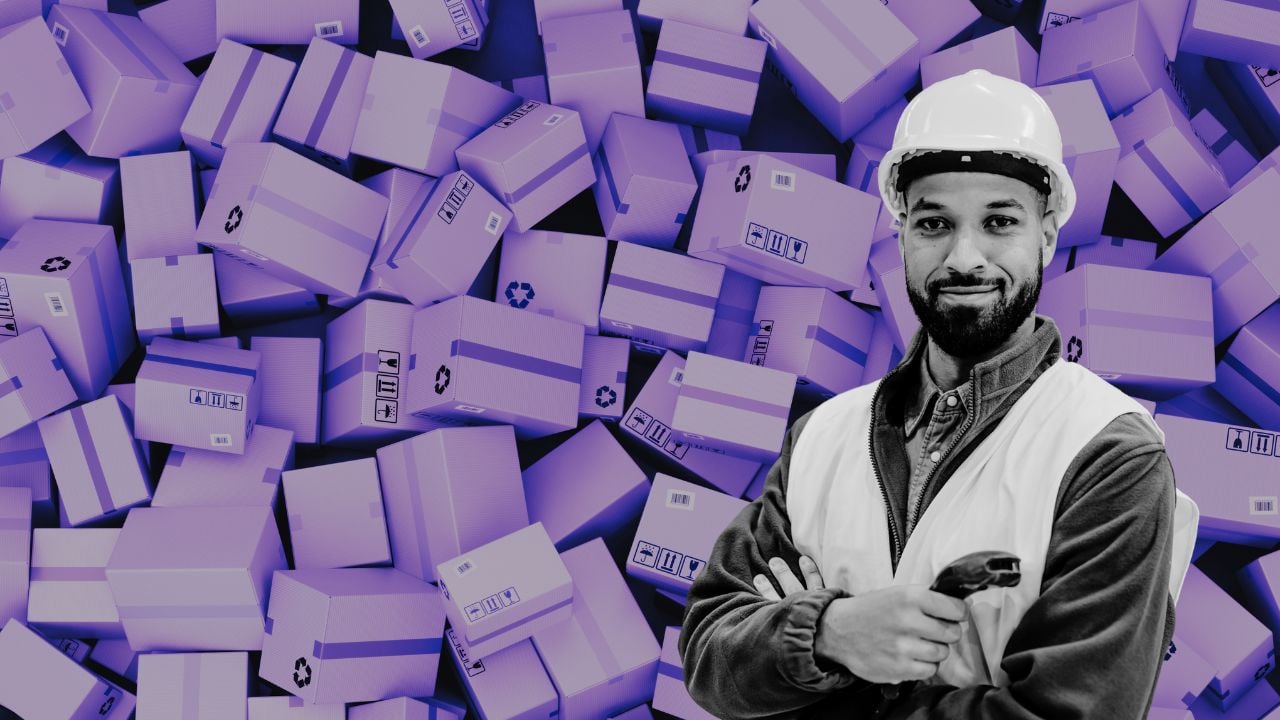
Retailers or brands using...
3PL warehouses can use omnichannel fulfillment to handle customer orders by tapping into inventory from any sales channel or location for additional flexibility and complete visibility.
Unlike multichannel fulfillment, where each channel operates separately, omnichannel combines them seamlessly. It covers everything from picking to packing to shipping, allowing orders to come from various sales channels and online platforms. This strategy prevents overstocking by allocating products from different stores and requires syncing data within a collaborative visibility platform for effective inventory management.
To make it straightforward, omnichannel fulfillment simply means giving consumers lots of ways to get what they buy.
Using unified commerce functionality, omnichannel fulfillment emphasizes inventory visibility and is all about being flexible and convenient for customers, making their shopping experience better overall. Providing availability information earlier leads to a decrease in cart abandonment rates and alleviates consumer frustration.
Omnichannel technological solutions not only offer detailed operational insights but also provide retailers with real-time access to comprehensive customer information. This includes purchase behavior, preferences, history, and feedback across all sales channels. Retailers can leverage this data to personalize recommendations and also enhance customer experiences with relevant products and services.
How does a WMS improve Omnichannel Fulfillment?
A WMS plays a pivotal role in enabling an omnichannel strategy by providing centralized inventory management, order routing, and fulfillment orchestration. It synchronizes inventory across channels, facilitates split shipments, and ensures consistent customer experiences, regardless of the sales channel. To put it simply, an omnichannel strategy can’t exist without a proper WMS in place to help with visibility, order management, fulfillment options, integrations, and overall consistent customer experiences.
Why 3PLs need Warehouse Management System (WMS) Automation:
Third party logistics (3PL) providers require Warehouse Management Systems (WMS) automation to optimize warehouse operations, improve inventory accuracy, and enhance order fulfillment efficiency. Automation streamlines processes such as receiving, picking, packing, and shipping, leading to cost savings and customer satisfaction.
- Order Processing: WMS automates order receipt and prioritization based on rules like urgency and inventory availability, ensuring swift fulfillment.
- Inventory Management: WMS integrates with inventory systems for real-time tracking, minimizing errors, and optimizing stock control.
- Task Assignment: WMS automates task allocation, ensuring equitable workload distribution and maximizing efficiency.
- Real-time Inventory Visibility: WMS provides real-time visibility into inventory levels and movements through technologies like barcode scanning and IoT sensors, enabling precise monitoring and informed decision-making.
- Efficient Inventory Management: WMS efficiently organizes inventory, assigns storage locations, and streamlines picking and packing processes for faster fulfillment.
- Accurate Inventory Accounting: WMS offers accurate inventory data for financial planning and reporting, facilitating better decision-making and resource utilization.
- Demand Forecasting: WMS utilizes demand forecasting tools to predict future inventory needs based on historical data and market trends, allowing businesses to adjust inventory levels proactively.
- Advanced Inventory Prediction: WMS leverages AI and ML to predict inventory needs with higher precision, optimizing inventory levels and improving supply chain efficiency.
Warehouse Management Systems and inventory management are closely connected in logistics and supply chain operations. WMS focuses on improving warehouse operations, enhancing inventory accuracy, optimizing resource use, and boosting efficiency in the warehouse environment. Check out more about the elements and the importance of WMS in an industry that’s moving away from ERPs.
Automated vs. Manual Supply Chain Operations:
Automation in supply chain operations offers numerous advantages over manual processes, including increased accuracy, faster order processing, reduced labor costs, and improved scalability. Manual operations, on the other hand, are prone to errors, inefficiencies, and limited scalability, hindering business growth.
- Comprehensive Warehouse Management: WMS platforms offer a comprehensive set of features designed to optimize every aspect of warehouse operations. These can include but are not limited to inventory management, order processing, receiving, put-away, picking, packing, and shipping. By automating and streamlining warehouse operations and processes, WMS software significantly enhances operational efficiency and productivity–from procurement to last mile.
- Inventory Optimization Strategies: WMS implements sophisticated inventory optimization strategies to maximize storage space utilization and minimize carrying costs. These strategies may include cycle counting, dynamic slotting, demand forecasting, and automated replenishment, ensuring optimal inventory levels while reducing waste and disregarded stock.
- Enhanced Order Fulfillment: WMS platforms streamline order fulfillment processes by automating tasks and optimizing picking routes and rate shopping. Using intelligent algorithms a WMS can analyze order data to determine the most efficient picking sequences, minimizing travel time and labor costs. This results in faster order processing, improved order accuracy, and enhanced customer satisfaction.
- Integration Capabilities: Integration with other supply chain management systems, such as Fulfillment Management Systems (FMS), enables seamless data connectivity and collaboration across various departments. This integration enhances supply chain visibility, facilitates accurate demand planning, and enables timely decision-making to drive overall supply chain efficiency.
The choice between manual and automated supply chain management greatly affects efficiency, accuracy, and profits. Manual processes rely on human effort for tasks like order processing and inventory management, offering flexibility but prone to errors and inefficiencies. Automation, on the other hand, uses technology to streamline operations, improving efficiency, accuracy, and scalability. It saves costs, boosts productivity, and enhances customer satisfaction.
Automation also improves visibility and transparency in the supply chain, providing real-time insights into inventory and order status. Integrated data enables data-driven decisions and quick responses to market changes. With automation, companies can optimize inventory, reduce stockouts, and enhance customer satisfaction. Overall, while manual processes offer flexibility, automation ensures efficiency, accuracy, and scalability, vital for modern supply chain management.
What is the future of supply chains?
The future of WMS lies in advanced technologies such as Artificial Intelligence (AI), Internet of Things (IoT), Machine Learning (ML), and predictive analytics. AI software is versatile, handling tasks like forecasting, inventory management, route planning, and operating automated equipment. As AI learning speeds up, expect even more uses to emerge. These innovations empower WMS to anticipate demand, optimize inventory placement, and enable real-time tracking, enhancing operational agility and responsiveness.
Omnichannel represents the future of the supply chain due to its ability to seamlessly integrate multiple sales channels and provide a cohesive shopping experience for customers. Here's why:
- Customer-Centric Approach: Omnichannel prioritizes the customer experience by allowing them to interact with a brand across various touchpoints, including online platforms, mobile apps, social media, and physical stores. This customer-centric approach enhances brand loyalty and satisfaction.
- Flexibility and Convenience: With omnichannel, customers enjoy the flexibility to choose their preferred purchasing channels and methods, whether it's ordering online, picking up in-store, or having items delivered to their doorstep. This flexibility enhances convenience and meets the diverse needs of modern consumers.
- Inventory Optimization: Omnichannel enables retailers to optimize their inventory management by consolidating stock across different channels. By having a centralized view of inventory, businesses can minimize stockouts, reduce excess inventory, and improve overall operational efficiency.
- Data-Driven Insights: By collecting and analyzing data from various channels, omnichannel supply chains gain valuable insights into customer behavior, preferences, and trends. This data-driven approach empowers businesses to make informed decisions, personalize marketing strategies, and forecast demand more accurately.
- Competitive Advantage: Embracing omnichannel allows companies to stay competitive in today's rapidly evolving retail landscape. Brands that offer seamless shopping experiences across channels are more likely to attract and retain customers, differentiate themselves from competitors, and drive sustainable growth.
Omnichannel focuses on customer-centricity, flexibility, inventory optimization, data-driven insights, and maintaining a competitive edge in the market. As consumer expectations continue to evolve, businesses must embrace omnichannel strategies to thrive in the digital era.
Modern WMS software offers real-time inventory tracking inside and outside the warehouse, ensuring accurate and up-to-date information across all channels. With features like cloud-based architecture and real-time visibility into fulfillment operations, WMS facilitates efficient order processing and reduces the risk of overselling or backorders.
WMS is essential for thriving omnichannel fulfillment due to its ability to provide real-time inventory visibility, streamline operations, and support seamless coordination across channels. As businesses scale, leveraging WMS ensures improved profitability, operational efficiencies, and enhanced customer experiences, ultimately driving sales and revenue growth.
How to seamlessly integrate Omnichannel Fulfillment with a Warehouse Management System (WMS):
To achieve seamless integration, businesses must prioritize compatibility between their omnichannel and WMS platforms. This involves leveraging APIs and integration tools to connect disparate systems, ensuring real-time data synchronization and operational visibility. Additionally, investing in customizable WMS solutions that cater to specific omnichannel requirements is crucial for optimizing fulfillment processes.
The Osa Collaborative Visibility Platform offers WMS solutions providing end-to-end visibility and breaking down data siloes within the supply chain. Our warehouse management system streamlines all e-commerce backend operations and integrations. Operating from a single platform supported by a network of tech-enabled warehouses. Unlock your WMS for omnichannel fulfillment today!