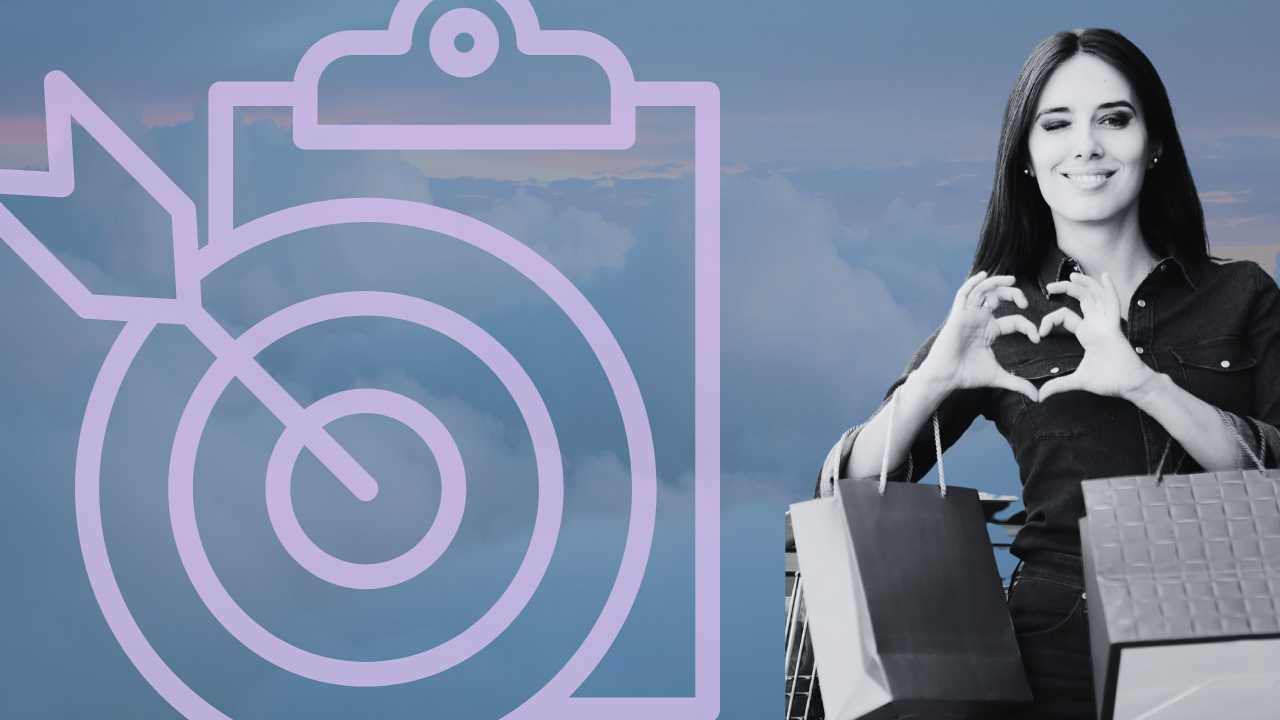
Order accuracy is not just a metric—it’s a fundamental aspect of a successful supply chain operation. Order accuracy refers to how precisely a company fulfills its customers' orders, ensuring that the right products reach the right customers in the right quantities and at the right time. As e-commerce continues to grow and consumer expectations rise, maintaining high order accuracy has become essential for businesses looking to stay ahead.
However, achieving and maintaining high order accuracy is a complex challenge. Various factors, from human error and inefficient processes to poor inventory management and external conditions like traffic and weather, can contribute to order inaccuracies. The impact of low order accuracy extends beyond simple mistakes—it can severely affect customer satisfaction, operational efficiency, and profitability. We will explore the concept of order accuracy, how to measure it, why it matters, and, most importantly, how to improve it.
Table of Contents
How to Calculate & Measure Order Accuracy?
Why Order Accuracy is Important?
How to Improve Order Accuracy?
Tracking KPIs to Improve Order Accuracy
What is Order Accuracy?
Order accuracy is a key performance indicator (KPI) in supply chain management that measures how accurately a company fulfills its orders. It reflects the percentage of orders shipped without any discrepancies between the order placed by the customer and the order delivered. This includes factors such as the correct product, quantity, size, color, and timely delivery.
Understanding Order Accuracy Rate (OAR) and Order Accuracy KPI
Order Accuracy Rate (OAR) is the most common way to quantify order accuracy. The order accuracy rate is calculated by dividing the number of accurate orders by the total number of orders processed, then multiplying by 100 to get a percentage:
For example, if a company processes 10,000 orders in a month and 9,700 of those orders are accurate, the OAR would be 97%. Achieving and maintaining an order accuracy rate above 99% is typically considered excellent and is the goal for most companies aiming to provide exceptional customer service.
However, it's essential to understand that order accuracy rates are not the only metric involved in evaluating order accuracy. Other related KPIs such as Order Entry Accuracy KPI and Order Fulfillment Accuracy KPI also play significant roles. The Order Entry Accuracy KPI refers to how accurately customer orders are entered into the system, while Order Fulfillment Accuracy KPI deals with how precisely the orders are picked, packed, and shipped.
Order Accuracy in Different Industries
Order accuracy can vary significantly across industries. For example, in the ecommerce sector, where customers expect fast and flawless deliveries, even a small mistake can lead to a poor customer experience. In contrast, in manufacturing, order accuracy might also involve ensuring that parts or components are delivered in the correct sequence or with the right specifications, which is critical for production efficiency. Understanding the nuances of order accuracy in your specific industry is crucial for setting the right standards and expectations.
How to Calculate & Measure Order Accuracy?
Calculating order accuracy starts with defining what constitutes an accurate order within your organization. This includes meeting customer expectations in terms of product type, quantity, quality, and delivery time.
Steps to Measure Order Accuracy
-
Define Accuracy Parameters
Establish what criteria define an accurate order. This might include correct item selection, appropriate quantity, proper packaging, and timely delivery. Make sure these criteria align with customer expectations and your operational goals. -
Track Accurate Orders
Keep a record of orders that meet all the accuracy parameters. This data is crucial for calculating the OAR and other relevant order accuracy KPIs. -
Calculate Order Accuracy Rate (OAR)
Use the formula provided earlier to calculate the OAR. This KPI will give you a clear picture of how well your order fulfillment process is performing. -
Monitor Related Order Accuracy KPIs
In addition to OAR, track other order accuracy KPIs such as Order Entry Accuracy KPI, Order Fulfillment Accuracy KPI, and Inventory Accuracy KPI. Monitoring these metrics provides a more comprehensive view of your order accuracy and helps identify specific areas for improvement. -
Regular Reporting and Analysis
Regularly report and analyze these KPIs to track trends over time. This will help you identify patterns, predict potential issues, and make data-driven decisions to improve order accuracy.
Real-World Ecommerce Example: Amazon Effect
A prime example of how critical order accuracy is can be seen with Amazon. The ecommerce giant has built its reputation on fast and accurate deliveries. Even when they aren’t always accurate, they maintain high customer loyalty by maintaining a customer-centric returns policy. By employing advanced technology such as robotics in their fulfillment centers, using real-time and visible inventory tracking, and continuously refining their processes, Amazon maintains high order accuracy rates, contributing to their success and customer loyalty.
Why Order Accuracy is Important?
Deliver Positive Customer Experiences
In the age of instant gratification, customers expect their orders to be fulfilled accurately and delivered quickly. An accurate order is a fundamental part of a positive customer experience. When customers receive what they ordered, they are more likely to be satisfied, which can lead to repeat business, positive reviews, and brand loyalty.
On the other hand, inaccurate orders can lead to frustration, dissatisfaction, and a damaged brand reputation. Customers today have numerous options, and a single mistake can drive them to competitors. The impact may be greater than you anticipate. Remarkably, 32% of customers would stop supporting a brand they love after just one negative experience. If negative interactions persist two or three more times, an overwhelming 92% of customers will completely sever ties with the company. On the other hand if a customer has a positive experience then 72% of customers are likely to share this experience with 6 people or more.
Pinpoint Weaknesses in Your Processes
High order accuracy is an indicator of a well-functioning order fulfillment process. Conversely, low order accuracy highlights weaknesses in the process. By tracking order accuracy, companies can identify specific areas where errors occur, whether it’s during order entry, picking, packing, or shipping.
For instance, if most errors are happening during the picking process, it might indicate a need for better inventory organization or more accurate labeling. Once these weaknesses are identified, they can be addressed through targeted improvements, such as process changes, employee training, or the implementation of new technologies.
Opportunities for Innovation
Improving order accuracy often involves adopting new technologies and processes. This can include automation, better inventory management systems, and advanced tracking tools. By innovating in these areas, companies can not only improve order accuracy but also enhance overall operational efficiency.
Customer Satisfaction
Customer satisfaction is directly linked to order accuracy. When customers receive the correct products on time, their trust in the brand increases, leading to repeat purchases and positive word-of-mouth. High order accuracy contributes to a seamless customer experience, which is crucial for building long-term relationships with customers.
Poor order accuracy can result in returns, refunds, and negative reviews, all of which can harm a company’s reputation and bottom line. Maintaining high customer satisfaction through accurate orders and customer forward return policies is essential for survival and growth.
Better Efficiency
Accurate orders mean fewer returns, exchanges, and complaints. This not only reduces the workload on customer service and logistics teams but also streamlines the entire supply chain. With fewer errors to correct, companies can focus on more value-added tasks, such as optimizing inventory levels, improving delivery times, and enhancing the customer experience.
By reducing order errors, a company can decrease the number of "rush" orders that need to be expedited to correct mistakes. This leads to more efficient use of resources, such as labor and transportation, and can result in significant cost savings.
Reduced Operational Costs
Every incorrect order comes with a cost, whether it’s the expense of return shipping, handling, restocking, or even the potential loss of a customer. By improving order accuracy, companies can reduce these costs and improve their margins.
In addition to the direct costs associated with incorrect orders, there are also hidden costs, such as the time and resources spent resolving customer complaints or investigating the root causes of errors. By minimizing these errors, companies can allocate their resources more efficiently and focus on growth and innovation.
How to Improve Order Accuracy?
Improving order accuracy requires a multi-faceted approach that addresses both the root causes of inaccuracies and the processes involved in order fulfillment. Here are some strategies to help improve order accuracy in your supply chain.
Identify the Problems
The first step in improving order accuracy is identifying the root causes of inaccuracies. This can involve conducting a thorough analysis of your order fulfillment process, from order entry to delivery. Common issues that lead to inaccuracies include human error, poor inventory management, and inefficient processes.
If inaccuracies are occurring during the picking process, it might be due to poorly organized inventory or unclear labeling. By identifying these issues, you can develop targeted strategies to address them. This might involve reorganizing your warehouse, implementing better training programs for your staff, or adopting new technologies to streamline the process.
Accounting for Road Conditions
External factors such as road conditions, traffic, and weather can also impact order accuracy, particularly for companies that handle their own deliveries. Investing in route optimization software can help mitigate these risks by planning the most efficient delivery routes and accounting for potential delays.
Better Labeling of Goods
Clear and accurate labeling is essential for preventing mistakes in the picking, packing, and shipping processes. Labels should include all relevant information, such as product name, SKU, quantity, and destination. Implementing a standardized labeling system can further reduce the chances of errors.
Proper Packaging of Goods
Proper packaging is another critical component of order accuracy. Ensuring that products are securely packed and labeled correctly minimizes the risk of damage during transit and ensures that the correct items reach the customer. Packaging materials should be chosen based on the type of product and its fragility.
Provide Clear Product Descriptions
Accurate and detailed product descriptions are crucial for reducing order errors. When customers have a clear understanding of what they are ordering, they are less likely to make mistakes, and the fulfillment team can ensure that the correct items are picked and packed.
Task Automation
Automation is one of the most effective ways to improve order accuracy. Automated systems can handle repetitive tasks such as order entry, picking, and packing with greater precision than humans, reducing the likelihood of errors. Automation can also streamline processes, making the entire fulfillment process more efficient.
Get Inventory Management Software
Effective inventory management is key to maintaining high order accuracy. Implementing advanced inventory management software can help track stock levels in real-time, prevent stockouts and overstocking, and ensure that the correct items are available for picking. This software can also integrate with other systems, such as order management and warehouse management systems, to provide a seamless flow of information.
Do Regular Checkups
Regularly reviewing and auditing your order fulfillment processes is essential for maintaining high order accuracy. This includes conducting inventory audits, reviewing order accuracy KPIs, and analyzing any discrepancies or issues that arise. By continuously monitoring and refining your processes, you can ensure that your order accuracy remains high.
Tracking KPIs to Improve Order Accuracy
Monitoring order accuracy key performance indicators (KPIs) is essential for pinpointing improvement areas and assessing progress in operational efficiency.
Inventory Turnover
Inventory turnover gauges the frequency with which a company's inventory is sold and replenished within a specific timeframe. High turnover often signifies efficient inventory management and robust product demand. However, excessively high turnover may result in stockouts, contributing to order inaccuracies.
Average Order Value
The average order value (AOV) is the average amount spent by customers on each order. By analyzing AOV, companies can gain insights into customer purchasing patterns and identify strategies to enhance order accuracy, such as offering bundled products or upselling complementary items.
Return Rate
The return rate reflects the percentage of orders returned by customers. Elevated return rates can signal underlying issues with order accuracy, including incorrect shipments or damaged goods. Addressing these issues to reduce return rates is vital for improving both order accuracy and customer satisfaction.
Average Shipping Time
Average shipping time is the time elapsed from order placement to customer delivery. Extended shipping times can increase the risk of order inaccuracies due to delays, missed deliveries, or damaged products. Streamlining shipping processes to reduce average shipping time is critical for improving overall order accuracy.
Order Picking Accuracy
Order picking accuracy assesses the precision with which items are selected from inventory and prepared for shipment. This KPI is closely linked to overall order accuracy, as picking errors are a primary source of order inaccuracies. Leveraging automated picking systems or improving workforce training can significantly boost order picking accuracy.
Conclusion
Order accuracy is a critical factor in the success of any business, particularly in the supply chain and logistics industry. By understanding the importance of order accuracy, identifying the root causes of inaccuracies, and implementing strategies to improve it, companies can enhance customer satisfaction, improve operational efficiency, and reduce costs.
Investing in advanced technologies such as inventory management software, route optimization software, and automation systems can significantly boost order accuracy and streamline the order fulfillment process. Additionally, regular training for employees and continuous monitoring of order accuracy KPIs are essential for maintaining high order accuracy over time.
As the demand for faster, more accurate deliveries continues to grow, companies that prioritize order accuracy will be better positioned to meet customer expectations and achieve long-term success in a competitive marketplace.
If your company is facing challenges with order accuracy, Osa can help you implement the right solutions to improve your order fulfillment processes and achieve higher levels of accuracy. Speak to a supply chain expert today to see how supply chain technology can help your logistics operations hit the target.