8 min read
Key Features of 3PL WMS Software for Efficient Warehousing
Chelsea Mori
:
November 5, 2024
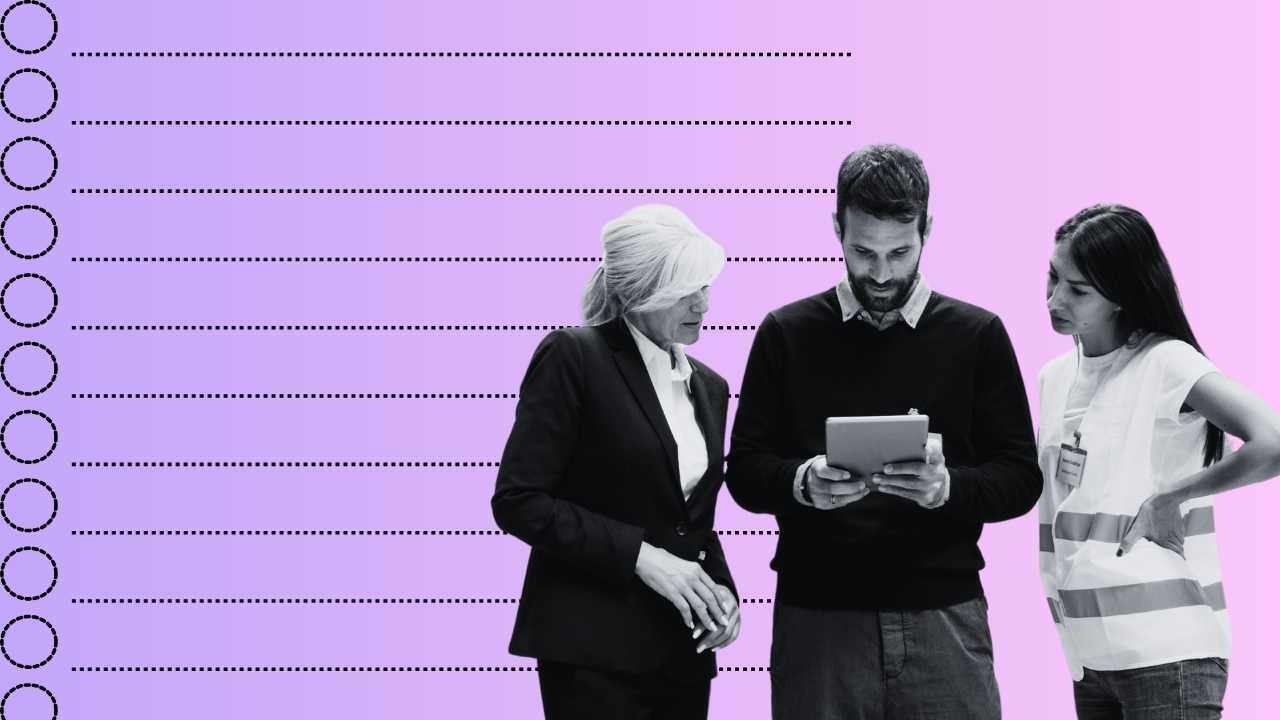
As e-commerce rapidly grows, so does the complexity of supply chains. Third-party logistics (3PL) providers, who help their brand and retailer customers with their omnichannel fulfillment needs, have been required to keep up to date with the most efficient solutions in order to streamline supply chain processes. For 3PLs looking to enhance efficiency and reduce operational costs, Warehouse Management Systems (WMS) have been clutch in meeting dynamic customer demands. From order processing to fulfillment, product sourcing, inventory management, last mile, and returns management, WMS software is a necessity.
What is a 3PL Warehouse Management System?
A Warehouse Management System (WMS) for 3PLs is technology that allows logistics providers and 3PLs to manage warehouse and logistics operations for multiple customers with a range of varying complexity. Most importantly, it centralizes and streamlines supply chain processes, including receiving goods, inventory management, order fulfillment, and shipping, to ensure that products flow smoothly through the supply chain. For 3PLs serving multiple clients, a WMS enables greater visibility, tracking, and coordination, helping businesses to meet demanding timelines, avoid stockouts, and maintain high service levels.
One key advantage of a 3PL WMS is its ability to offer collaborative visibility. By consolidating data from multiple sources, the system enables all stakeholders, from suppliers to retailers, to access real-time inventory information, allowing better decision-making and quicker response to changes in demand or supply chain disruptions. This transparency also enables 3PLs to provide clients with accurate, up-to-date reports and insights, promoting trust and enhancing client satisfaction.
Advanced 3PL WMS platforms, like offered in the Osa Collaborative Visibility Platform, integrate seamlessly with other systems, such as e-commerce platforms, ERPs, and customer service systems. This connectivity allows businesses to automate various processes and streamline order management across all channels, reducing manual work and the risk of errors. As e-commerce and omnichannel retail continue to grow, a robust WMS is essential for 3PLs to keep up with the increased complexity of fulfillment and maintain a competitive edge
How WMS Software Helps 3PLs
The third-party logistics (3PL) market, which was estimated at $247.4 billion in 2023, continues to rapidly evolve. 3PL WMS platforms offer logistics providers and their partners the opportunity to grow and enhance supply chains along with it. Key ways WMS technology technology enhances supply chain management include:
Improved Efficiency and Reduced Labor Costs
WMS technology automates routine tasks including inventory tracking and order picking, reducing manual labor and associated costs. This automation allows 3PLs to handle higher volumes with fewer errors, improving overall service quality.
Real-Time Inventory Visibility
With WMS software, 3PLs are able to offer up-to-date insights into stock levels and order status, enhancing transparency and reducing the risk of stockouts or overselling. This level of visibility improves decision-making and client satisfaction by offering greater control over inventory.
Scalability and Flexibility
A robust WMS adapts to growth, allowing 3PLs to scale operations in response to increasing demand. Modern WMS technology should include integration capabilities with other systems, supporting flexibility across multiple clients and markets—which is essential for omnichannel fulfillment.
Enhanced Customer Experience
By speeding up fulfillment processes and reducing errors, WMS technology ensures more accurate and faster deliveries, crucial for retaining customers and meeting modern service expectations.
Essential Features for a 3PL WMS
The purpose of warehouse management software is to boost operational efficiency, improve accuracy, and enhance scalability. The following features are essential for third-party logistics providers to manage complex, high-volume supply chain operations at peak performance.
Multi-Client Management
WMS platforms allow 3PLs to handle inventory, billing, and fulfillment for multiple clients within a single platform, ensuring accurate management of diverse client needs. 3PLs who use a WMS with multi-client management functionality can create individual profiles and customized settings to build separate operational rules and workflows for:
- Storage locations
- Inventory segmentation
- Picking rules
- Packing and packing rules
- Value added services
- Shipping requirements
- Billing and invoicing
Real-Time Inventory Tracking
3PL warehouse software gives instant visibility into stock levels and locations, enabling quick responses to inventory changes and reducing errors in order fulfillment. Real-time tracking on inventory by individual customers offers better accuracy to prevent stockouts or overstocking. 3PLs will see improved cost management and offer transparency to their customers from tracking SKUs, picking, receiving, and storage. Some key inventory management features include:
- Stock Keeping Units (SKU) management
- IoT and scanner functionality to reduce errors
- Warehouse and replenishment tasks (FIFO, FEFO)
- Batch and date updates
- Inventory movement and allocation reporting
Automated Order Fulfillment
Omnichannel fulfillment is a major growth driver for 3PLs. Utilizing WMS automation speeds up the picking, packing, and shipping processes, increasing efficiency and accuracy in handling high volumes of orders—regardless of sales channel. 3PL warehouse management systems with unified commerce are able to quickly distribute orders and reduce the amount of time and resources required to complete tasks. Coupled with multi-client management, specific rules for inventory, picking, packing and more can be automated through scanners and walk-through workflows to reduce manual errors. Features to look for:
- Data analytics for better forecasting
- Bulk order management
- Backlog management
- Automation rules for common tasks
- Order tracking, response logs, and details
- Updates for order receipts, dispatch, and status across channels
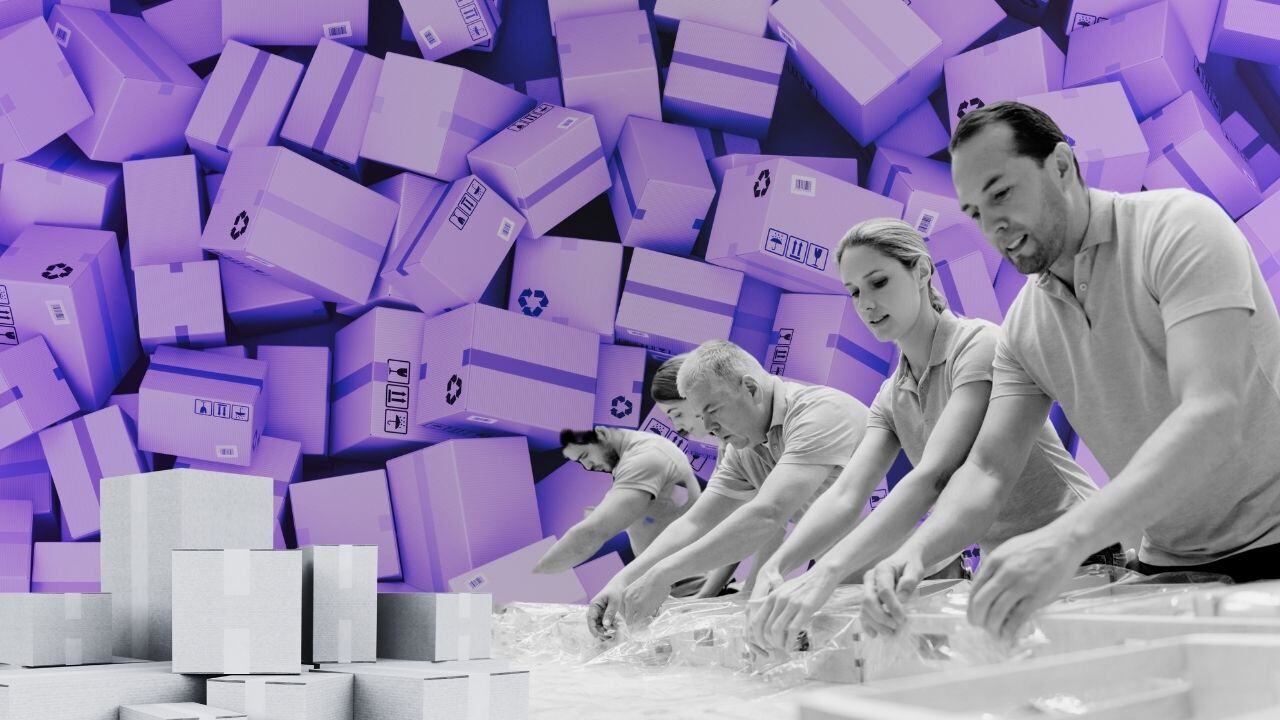
The Order Fulfillment Process: Definition, Steps, & Benefits for Supply Chain Management
Integration Capabilities
Tech-agnostic WMS technology with integration management is a game changer for 3PLs. It provides a holistic approach that enables more efficient coordination between warehouse workers, supply chain management systems, and logistics partners. While many warehouse management systems have standard integrations, custom integrations are a requirement to meet the needs of many e-commerce or omnichannel customers. The need seamless integrations Some include:
- Pre-built integrations to shopping carts and carriers
- Open API integrations for customized solutions
- EDI integrations for retailers
- Billing and invoicing systems
- ERP systems
- TMS, last mile, returns management
Advanced Shipping and Returns Management
Streamlining shipment tracking and return handling is essential for managing reverse logistics and providing efficient customer service. 3PLs will need a WMS that utilizes integrations to automate carrier selections and rate shopping. In addition, WMS functionality should offer end-to-end visibility for order and package details, the creation of shipping documentation, and bulk label and return tracking. Efficient returns management is an inevitable part of supply chain management as well. Key features to consider are:
- Integrated rate shopping and carrier selection
- Automated receipt and tracking information
- Returns against a blind receipt
- Return reasons and actions
- Reporting and analytics
Robust Reporting and Analytics
3PLs track performance metrics to make data-driven decisions, which improves operational efficiency and client satisfaction. The need for WMS technology to offer dynamic reporting and trend analysis is required to improve almost every aspect of 3PL performance. 3PLs must be able to monitor service level agreements (SLAs) and key performance metrics (KPIs) to meet customer expectations, understand how to optimize operations, and help improve financial and bottom-line performance. Artificial intelligence (AI) coupled with a WMS offers a comprehensive view of your entire supply chain network and forecasting.
- Scheduled reporting and analytics by customer
- AI-enables data for inventory forecasting and informed business decisions
- End-to-end operational reporting
- Real-time access to data for inventory, stock adjustments, orders, and deliveries
- Trend based analytics
3PL Billing and Accounting Integration
Third-party logistics is largely transactional. 3PLs must be able to bill, by client, for fulfillment activities and services. WMS technology allows for streamlined billing by tracking transactional data from all fulfillment activities, ensuring transparent and accurate invoicing. Data for activities should also track back to a customer in real-time to automatically generate invoices. Key billing features for a 3pl WMS include:
- Integrations with billing and invoicing software such as Sage, Quickbooks, or Netsuite
- Capture of transactional data in real-time
- Automatic generated invoices
- Capability to set up value added services by customer
- Custom charge codes and billing rules
- Draft and final billing
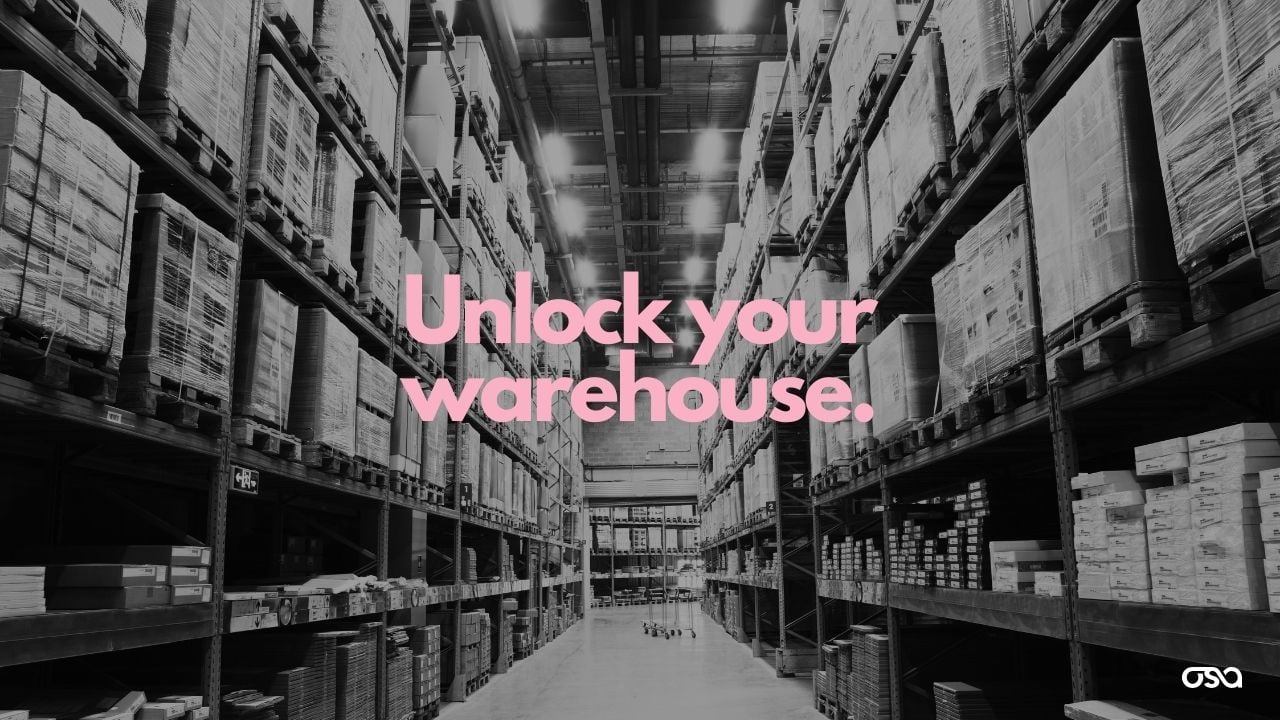
WMS for Accounting Visibility and Accuracy
Leave the ERP in the past and see how a WMS can change the way your 3PL stays one step ahead in the financial game. See our breakdown here.
Challenges Faced by 3PLs Without WMS
Third-party logistics (3PL) providers that operate without a Warehouse Management System (WMS) often encounter significant challenges that hinder their operational efficiency, customer satisfaction, and overall growth potential. In fact, only one third of 3PL warehouses and facilities do not use WMS. The lack of advanced technology can greatly impact a 3PL ability to attract new clients, scalability, and remain competitive in the marketplace. The most common challenges to impact 3PL are:
Inventory Inaccuracy
Without a WMS, tracking inventory in real-time becomes difficult, leading to inaccurate inventory records. This can result in stockouts or overstocking, both of which disrupt the supply chain and can erode customer trust.
Low Efficiency and High Labor Costs
Manual tracking and management of inventory are labor-intensive and prone to human error. These inefficiencies increase labor costs and lead to slower order fulfillment times, negatively impacting profitability and client satisfaction.
Limited Scalability
As a 3PL provider grows, the volume of orders and SKUs can quickly overwhelm manual processes. Without a WMS, scaling operations to meet client demands is challenging, often leading to bottlenecks during peak periods.
Poor Visibility and Tracking
Clients today expect real-time visibility into their inventory and order statuses. Without a WMS, 3PLs struggle to provide transparency, which leads to communication challenges and a lack of trust in the logistics process.
Increased Risk of Errors in Order Fulfillment
The absence of automated order management can lead to mistakes in order processing, picking, and shipping. These errors result in returns, delays, and reduced client satisfaction, which impact a 3PL provider's reputation.
The lack of WMS technology will largely leave 3PLs with poor data quality, ineffective operations, lack of system capabilities, inability to integrate for e-commerce and omnichannel fulfillment, and missed business and growth opportunities.
Advantages of Implementing a 3PL Warehouse Management System
WMS technology helps logistics businesses focus on their core strengths and use their labor resources and efforts in the most efficient ways. The ability to automate processes, remove manual errors, and enhance supply chain visibility helps 3PLs avoid costly mistakes. Here are the main advantages of using a WMS:
Improved Accuracy
One of the primary advantages of implementing a 3PL Warehouse Management System (WMS) is the enhanced accuracy in managing inventory and order fulfillment. By using automation and real-time tracking, a 3PL WMS reduces human error, streamlines data input, and provides clients with up-to-date visibility into their stock levels. With tools like barcode scanning and RFID, these systems improve the precision of picking, packing, and shipping processes, ensuring that orders are fulfilled correctly and timely. Accurate inventory management helps reduce overstocking or understocking, ultimately lowering costs and ensuring clients’ needs are consistently met.
Increased Efficiency
Efficiency is a significant benefit of integrating a 3PL WMS, especially for businesses handling large volumes of orders. These systems automate routine tasks, such as inventory tracking and order processing, which decreases the need for manual intervention and minimizes delays. Automation also enables quicker order fulfillment, optimized space utilization, and a reduction in labor costs by streamlining processes within the warehouse. The system’s ability to centralize data in real-time ensures that everyone from warehouse staff to customer service teams has the information they need instantly, leading to faster decision-making and better overall performance.
Scalable Solutions for Expansion
As 3PL businesses grow, the demands on their warehousing and logistics operations expand as well. A 3PL WMS offers scalability that supports the gradual or rapid growth of a company. These systems are designed to handle increasing inventory volumes, additional SKUs, and higher order frequencies, allowing businesses to adjust to seasonal peaks or market expansions without overhauling their entire system. Additionally, many 3PL WMS solutions are flexible, allowing users to integrate new technology as it emerges. This scalability empowers businesses to respond swiftly to demand changes, keeping them competitive and adaptive in a fast-paced industry.
Enhanced Client Satisfaction
For any 3PL provider, client satisfaction is crucial, and a robust WMS plays an essential role in achieving this. With real-time inventory visibility, clients can monitor their stock levels and order statuses directly through the system, which fosters transparency and builds trust. Additionally, a WMS’s accuracy and efficiency in managing orders lead to reduced errors, fewer returns, and faster shipping times. All of these factors contribute to improved client satisfaction, as clients are better able to meet their own customers’ expectations. A WMS can even support customized reporting, enabling clients to analyze key metrics and make informed decisions about their inventory management strategies.
By implementing a 3PL WMS, providers can benefit from improved accuracy, operational efficiency, scalability for growth, and enhanced client satisfaction, making it a worthwhile investment for any logistics-focused business.
The Future of 3PL Warehouse Management Systems
As e-commerce and omnichannel fulfillment continue to expand, third-party logistics providers and the need for technology will evolve alongside it. The role of Warehouse Management Systems (WMS) is becoming increasingly strategic—and required. Advances in artificial intelligence, machine learning, and IoT are no longer just concepts but integral aspects of 3PL operations, driving efficiency and creating resilience within the supply chain. These emerging technologies allow 3PL providers to forecast demand, optimize inventory levels, and enhance last-mile delivery—essential in an era where consumer expectations are higher than ever.
Looking forward, WMS solutions will likely become even more integrated with broader supply chain systems, supporting real-time decision-making and offering a unified view of inventory across multiple channels. Sustainability requirements and goals will also drive innovations within WMS, enabling 3PLs to manage resources more effectively and reduce environmental impacts.
For businesses relying on 3PL services, the future holds opportunities to achieve seamless, agile logistics through smarter, data-driven WMS platforms. By embracing these innovations, companies can stay competitive, responsive, and prepared for the unpredictable future of global supply chains.